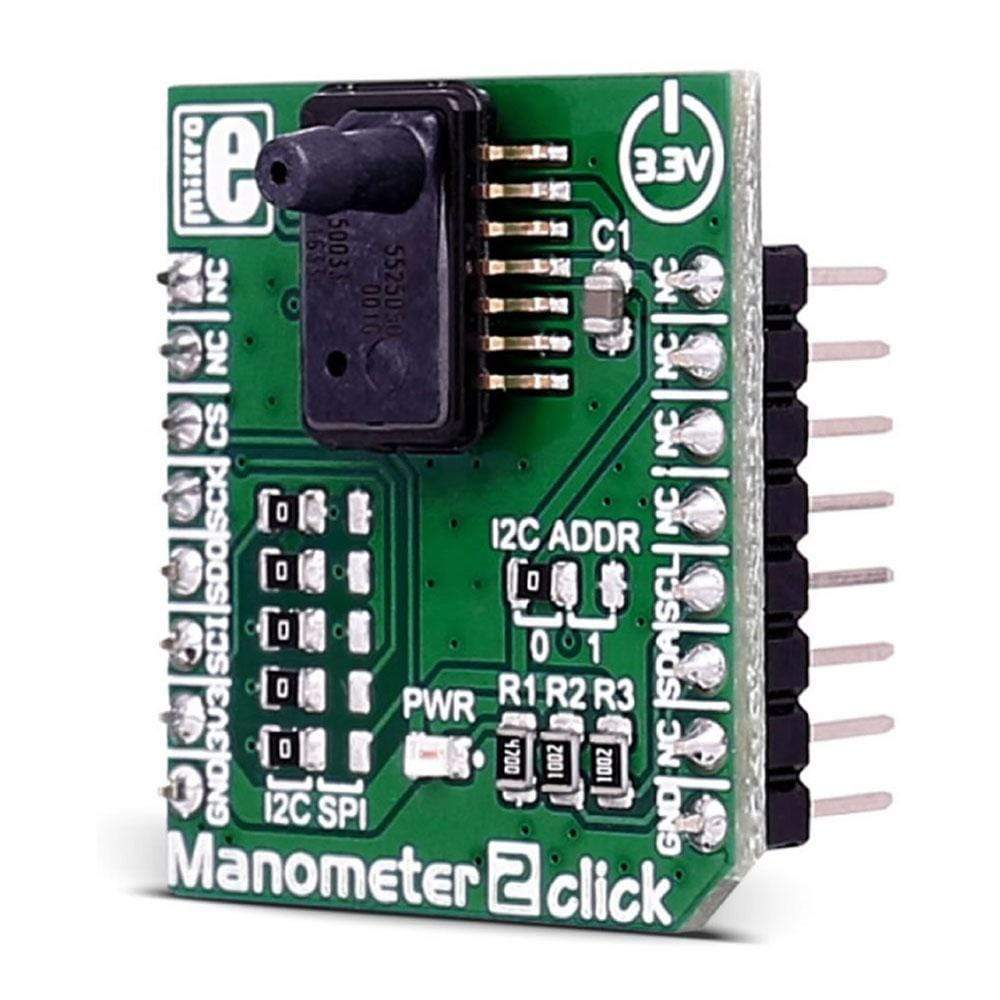
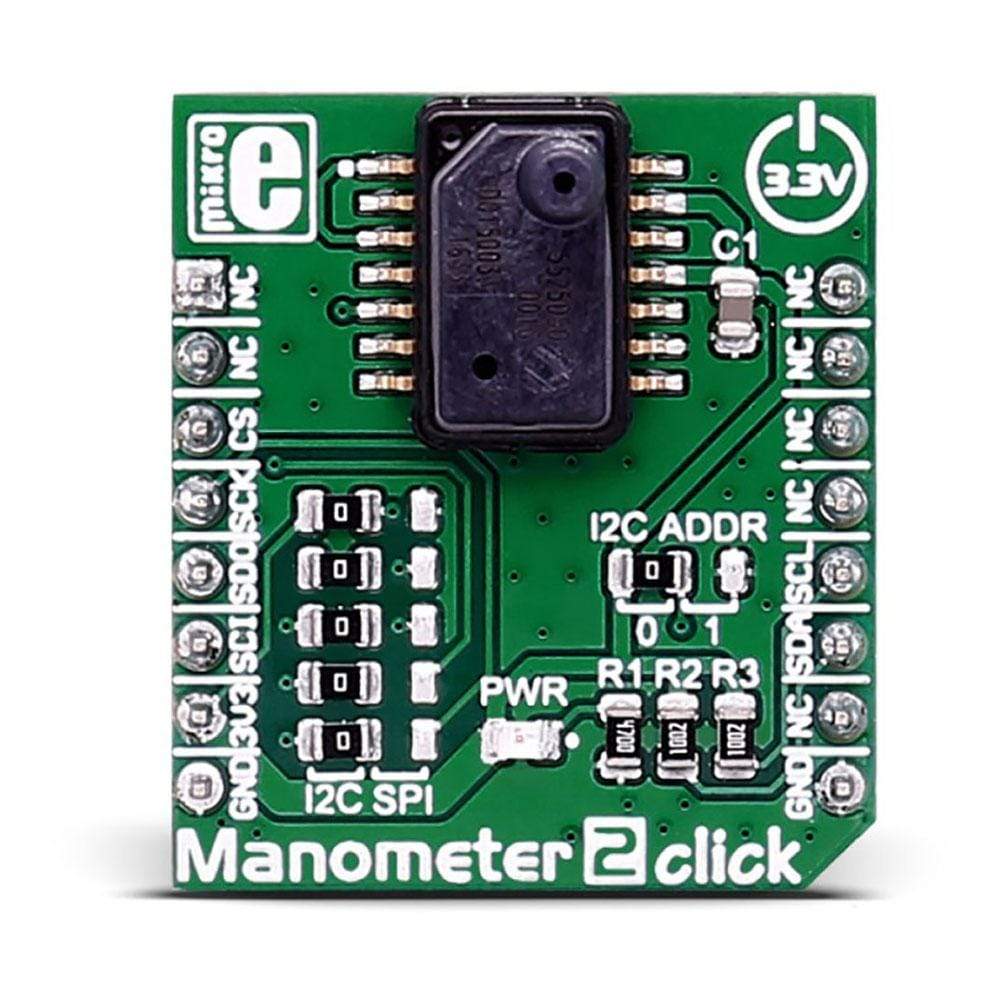
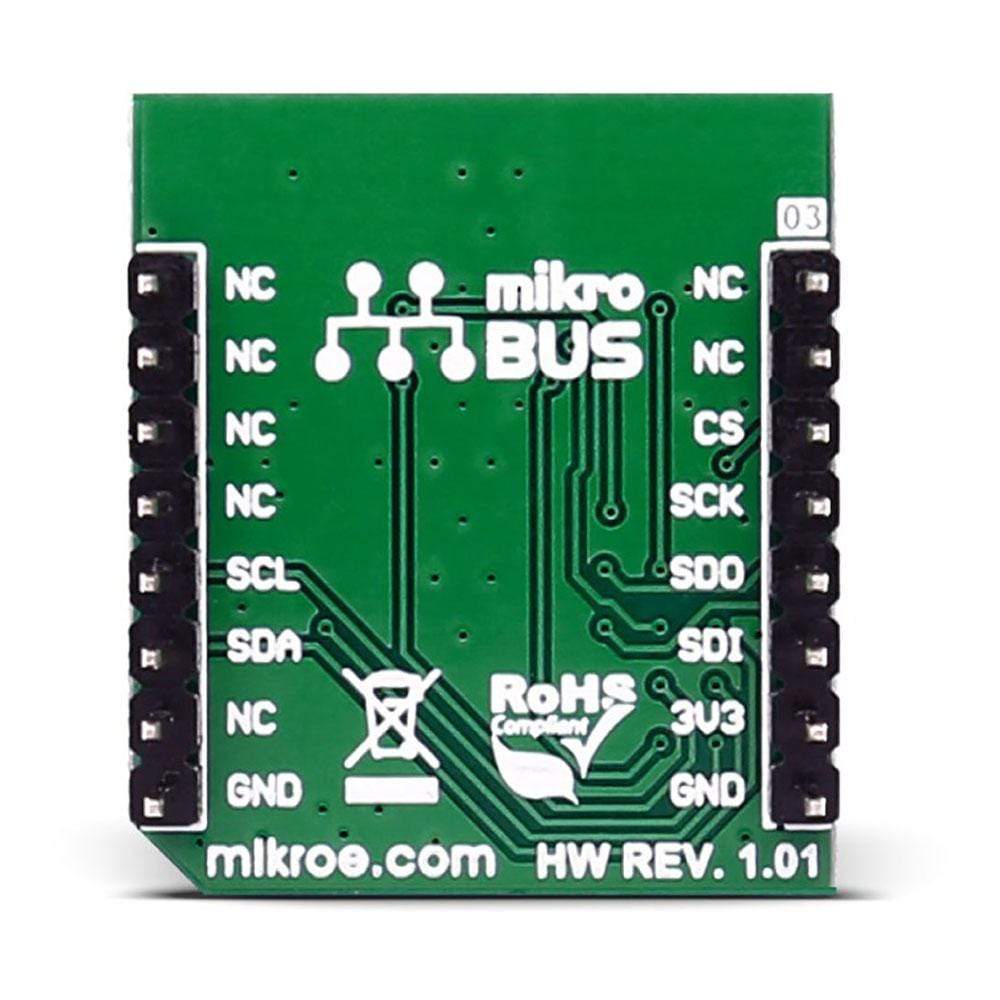
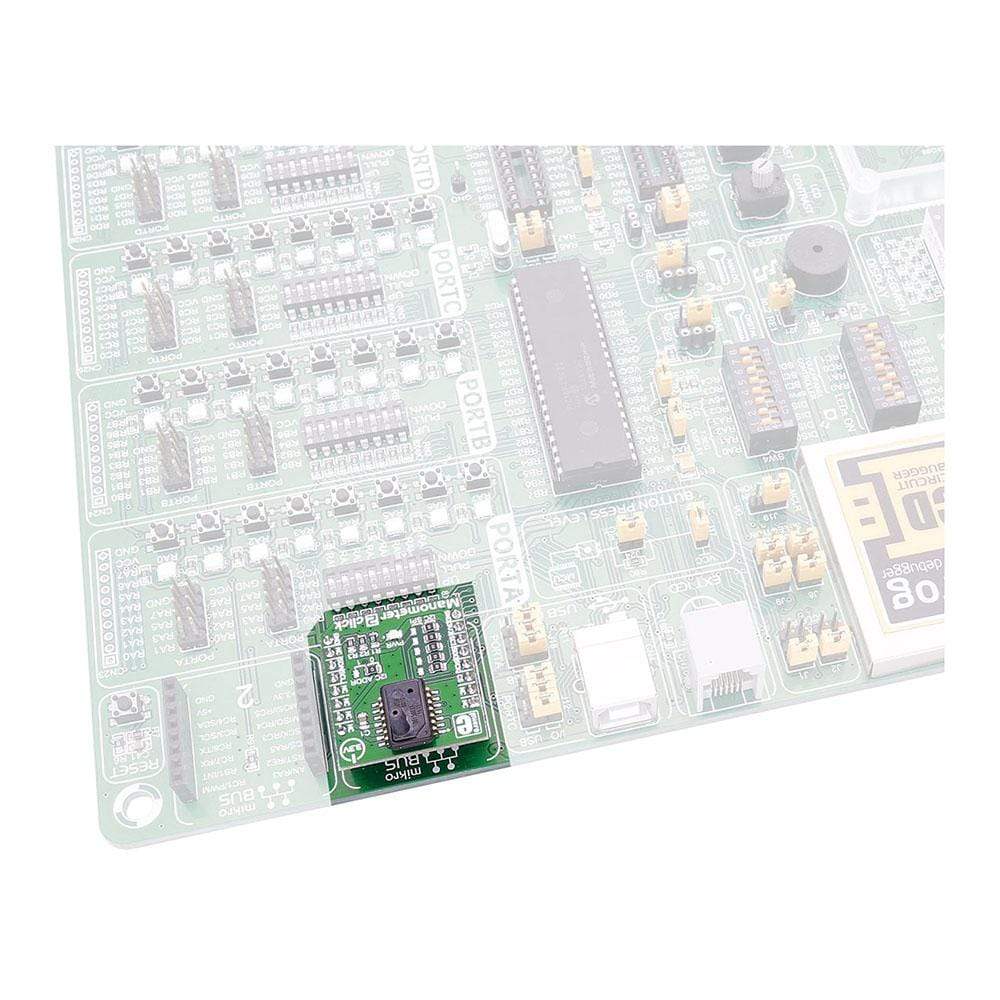
Overview
The Manometer 2 Click Board™ is based on the MS5525DSO-SB001GS digital pressure sensor, based on leading MEMS technology. The Click Board™ is designed to run on a 3.3V power supply. It communicates with the target microcontroller over I2C or SPI interface.
General Information | |
---|---|
Part Number (SKU) |
MIKROE-2550
|
Manufacturer |
|
Physical and Mechanical | |
Weight |
0.018 kg
|
Other | |
Country of Origin |
|
HS Code Customs Tariff code
|
|
EAN |
8606018710973
|
Warranty |
|
The Manometer 2 Click Board™ carries the MS5525DSO digital pressure sensor, based on leading MEMS technology. The Manometer 2 Click Board™ is designed to run on a 3.3V power supply. It communicates with the target microcontroller over I2C or SPI interface.
MS5525DSO Features
The MS5525DSO is a new generation of Digital Small Outline pressure sensors with SPI and I2C bus interface designed for high volume OEM users.
The sensor module includes a pressure sensor and an ultra-low power 24-bit ∆Σ ADC with internal factory calibrated coefficients. It provides a 24-bit digital pressure and temperature value and different operation modes that allow the user to optimize for conversion speed and current consumption.
The MS5525DSO consists of a piezo-resistive sensor and a sensor interface IC. The main function of the MS5525DSO is to convert the uncompensated analog output voltage from the piezo-resistive pressure sensor to a 24-bit digital value, as well as providing a 24-bit digital value for the temperature of the sensor.
How Does The Manometer 2 Click Board™ Work?
The Manometer 2 Click Board™ measures absolute pressure of 1PSI max, trough the barbed port.
You can choose between SPI and I2C communication.
SPECIFICATIONS
Type | Pressure |
Applications | Factory automation, altitude and airspeed measurements, medical instruments, leak detection, etc. |
On-board modules | MS5525DSO digital pressure sensor |
Key Features | sensor module includes a pressure sensor and an ultra-low power 24-bit ∆Σ ADC with internal factory calibrated coefficients |
Interface | I2C,SPI |
Compatibility | mikroBUS |
Click board size | S (28.6 x 25.4 mm) |
Input Voltage | 3.3V |
PINOUT DIAGRAM
This table shows how the pinout of the Manometer 2 Click Board™ corresponds to the pinout on the mikroBUS™ socket (the latter shown in the two middle columns).
Notes | Pin | ![]() |
Pin | Notes | |||
---|---|---|---|---|---|---|---|
NC | 1 | AN | PWM | 16 | NC | ||
NC | 2 | RST | INT | 15 | NC | ||
Chip Select | CS | 3 | CS | TX | 14 | NC | |
SPI Clock | SCK | 4 | SCK | RX | 13 | NC | |
SPI Master Input Slave Output | MISO | 5 | MISO | SCL | 12 | SCL | I2C Clock |
SPI Master Output Slave Input | MOSI | 6 | MOSI | SDA | 11 | SDA | I2C Data |
Power supply | +3.3V | 7 | 3.3V | 5V | 10 | NC | |
Ground | GND | 8 | GND | GND | 9 | GND | Ground |
JUMPERS AND SETTINGS
In order to set the SPI interface, you need to move all the 5 jumpers (JP1-JP5).
These jumpers are soldered in I2C interface position by default.
There is an option to select the alternate address with jumper J6 in the case of I2C interface (default position is logic 0).
Frequently Asked Questions
Have a Question?
Be the first to ask a question about this.