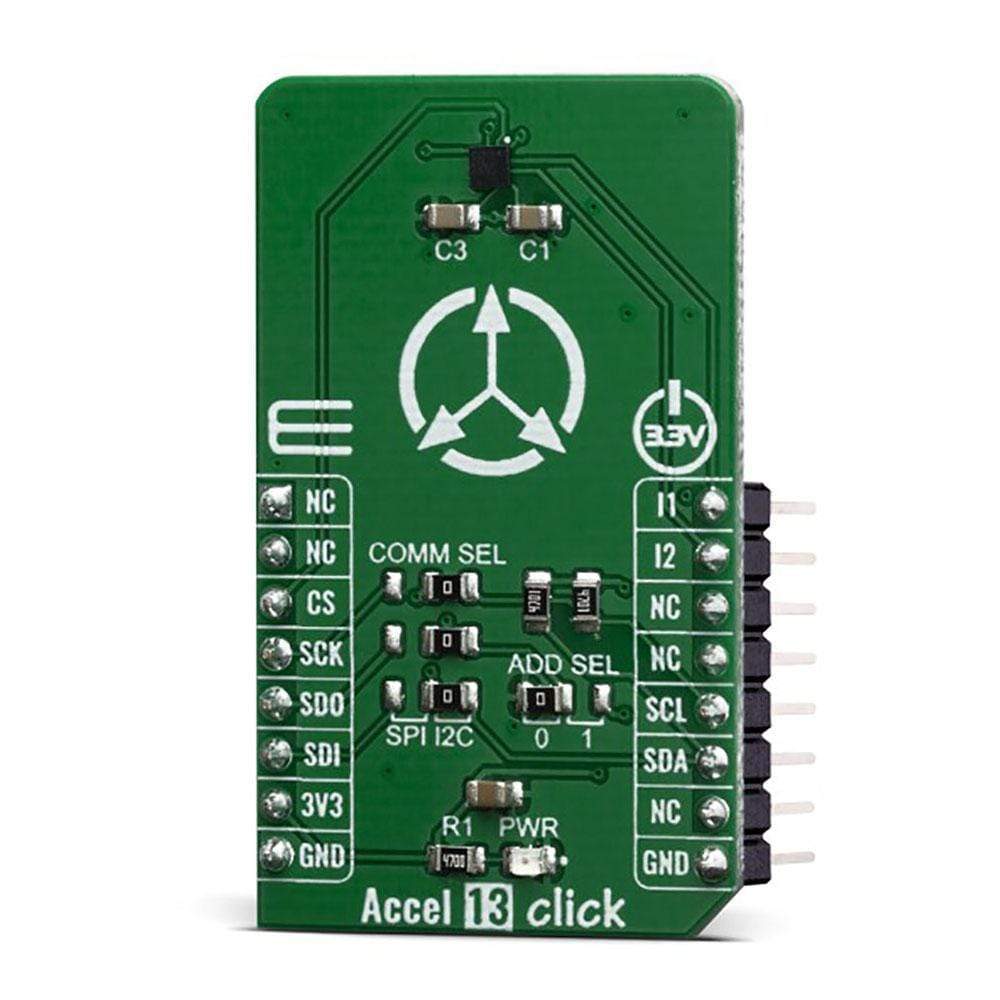
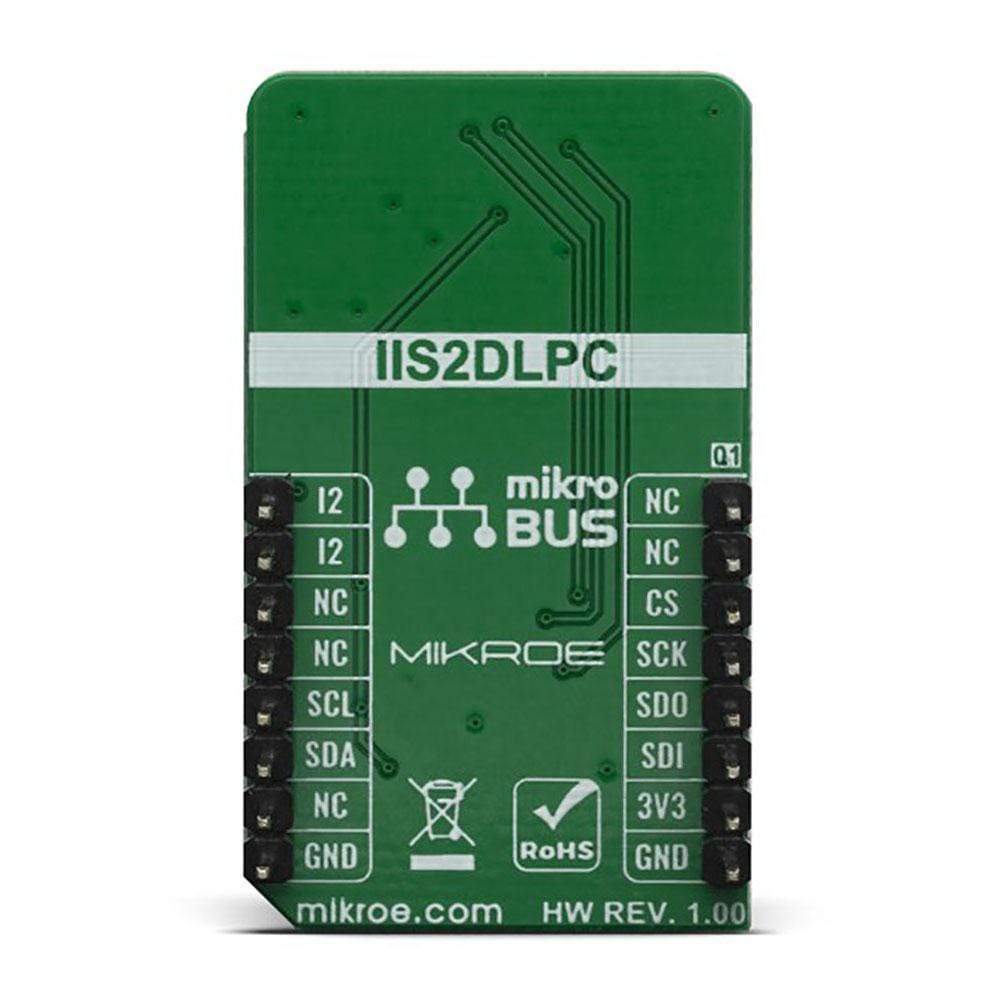
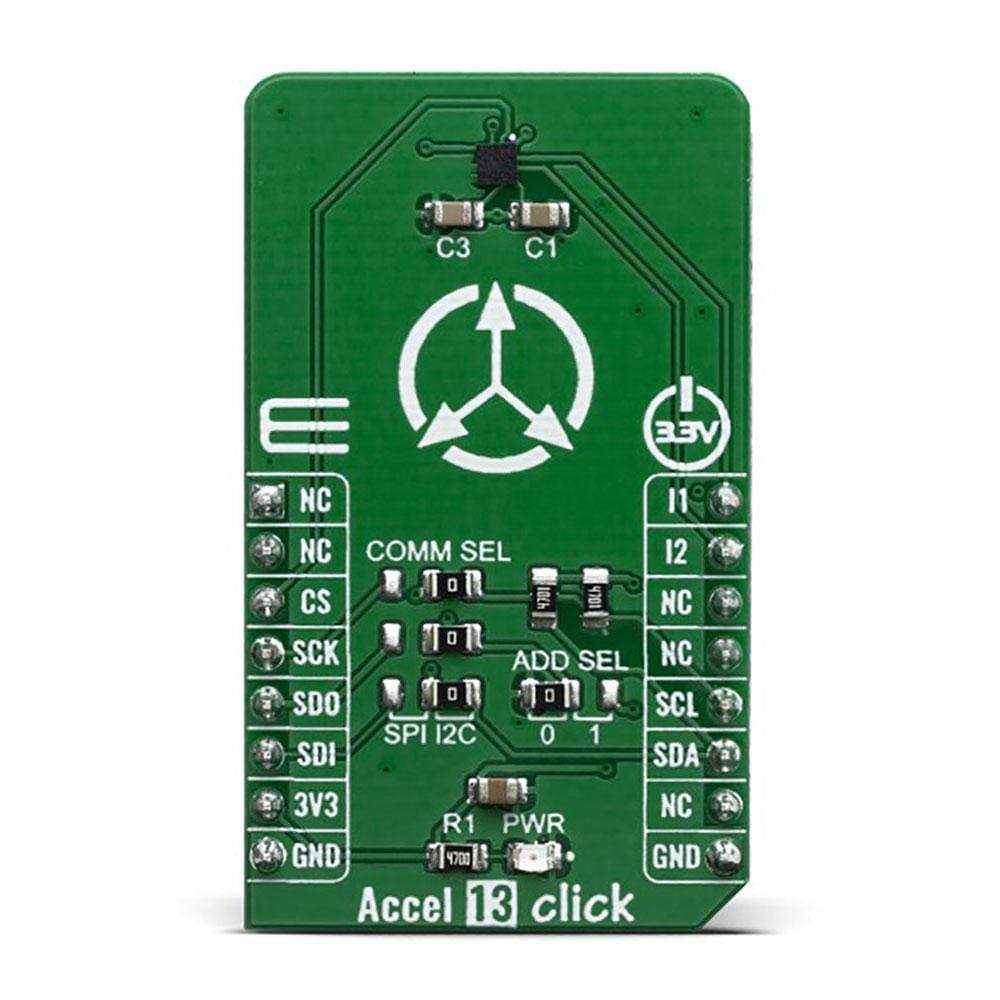

Overview
L' Accel 13 Click Board™ est doté d'un capteur accéléromètre triaxial à très faible consommation d'énergie avec intelligence intégrée, appelé IIS2DLPC. Ce Click Board™ permet des mesures de mouvement linéaire et de force gravitationnelle dans des plages de ±2 g, ±4 g, ±8 et ±16 g sur trois axes perpendiculaires. Ce capteur intelligent permet à l' Accel 13 Click Board™ de détecter de nombreux événements différents, notamment les appuis, les doubles appuis, le comptage des pas, la reconnaissance d'activité (marche, course, arrêt), le changement d'activité (tout type de changement de modèle d'accélération), l'orientation, etc. Il dispose d'un traitement de données intégré, offrant les données d'accélération directement, via l'interface standard I2C ou SPI.
General Information | |
---|---|
Part Number (SKU) |
MIKROE-3742
|
Manufacturer |
|
Physical and Mechanical | |
Weight |
0.018 kg
|
Other | |
Country of Origin |
|
HS Code Customs Tariff code
|
|
EAN |
8606018716906
|
Warranty |
|
With the total height of 0.7mm, the IIS2DLPC is well suited for using it in handheld or other space limited devices. Its powerful event detection engine is equipped with a set of features suitable for a wearable device, including free-fall, wakeup, highly configurable single/double-tap recognition, activity/inactivity, stationary/motion detection, portrait/landscape detection, and 6D/4D orientation. The sensor can use any of its two interrupt pins to report a detected event. The Accel 13 Click Board™ can be used for a rapid development and testing of various applications based on step counting, fitness applications, profile switching and display ON/OFF applications, angle measurement applications, and similar applications.
How Does The Accel 13 Click Board™ Work?
The Accel 13 Click Board™ is based on the IIS2DLPC, a high-performance ultra-low-power 3-axis accelerometer for industrial applications, from STMicroelectronics. This sensor has many features perfectly suited for wearables, handheld, and IoT applications, offering a good balance between the performance and the power consumption. One of its key features is its extremely low-power consumption, which makes it perfectly suited for such applications. There are several power modes which the IIS2DLPC device can use. While in low-power mode, the device consumes the least power, but the access to some features is restricted. More information can be found within the IIS2DLPC datasheet.
The IIS2DLPC sensor can measure acceleration within ranges of ±2 g, ±4 g, ±8, and ±16 g. It can output the measurement data using the Output Data Rate (ODR) from 1.6Hz (low-power mode), up to 1600Hz (Performance mode). A high-precision analog front end facilitates highly sensitive MEMS, featuring a 14-bit A/D Converter. It allows very high accuracy of the output, even during very low amplitude changes. This makes the sensor particularly sensitive and accurate with movements that generate relatively low acceleration signals. However, using a highly sensitive MEMS makes the IIS2DLPC prone to damage caused by extremely high g-forces (10,000 g for less than 200 µs).
Acceleration data is available in 14-bit format from both the data registers and the internal FIFO buffe, which can can memorize 32 slots of X, Y and Z data. The FIFO buffer can be used for more complex calculations or timed readings, reducing the traffic on the communication interface. The interrupt engine facilitates the FIFO buffer, triggering an interrupt for two FIFO events: watermark event, and FIFO buffer full event. FIFO buffer allows optimization within the firmware that runs on the host MCU.
Besides the acceleration MEMS and complementary analog front-end circuit, the IIS2DLPC sensor also has an integrated temperature sensor. It is updated up to 25 times per second, and sampled to an 12-bit value (complement of 2's format).
Interrupts can be triggered for many different events. Some basic events include the data-ready interrupt event and aforementioned FIFO events, while so-called feature engines can trigger an interrupt for any of the detected motion/movement events, including step detection/counter, activity recognition, tilt on wrist, tap/double tap, any/no motion, and error event interrupt. The extensive interrupt engine can use two programmable interrupt pins. Both of these pins can be assigned with any interrupt source and can be either LOW or HIGH on interrupt, depending on settings in appropriate registers. These two pins are routed to PWM and INT pin of the mikroBUS, and are labelled as IT1 and IT2, respectively.
The Accel 13 Click Board™ offers two communication interfaces. It can be used with either I2C or SPI. The onboard SMD jumpers labelled as COMM SEL allow switching between the two interfaces. Note that all the jumpers have to be positioned either I2C or to SPI position. When I2C interface is selected, an additional SMD jumper labelled as ADDR SEL becomes available, determining the least significant bit of the IIS2DLPC I2C address. The Click Board™ should be interfaced only with MCUs that use logic levels of 3.3V.
SPECIFICATIONS
Type | Motion,Acceleration |
Applications | Accel 13 Click Board™ can be used for a rapid development and testing of various applications based on step counting, fitness applications, profile switching and display ON/OFF applications, angle measurement applications, and similar applications. |
On-board modules | IIS2DLPC, a 14-bit triaxial acceleration sensor with ultra-low-power consumption, from STMicroelectronics. |
Key Features | Free-fall detection, wakeup, highly configurable single/double-tap recognition, activity/inactivity, stationary/motion detection, portrait/landscape detection, and 6D/4D orientation, ultra-low-power consumption, thermal readings |
Interface | GPIO,SPI,I2C |
Compatibility | mikroBUS |
Click Board™ size | M (42.9 x 25.4 mm) |
Input Voltage | 3.3V |
PINOUT DIAGRAM
This table shows how the pinout on Accel 13 Click Board™ corresponds to the pinout on the mikroBUS socket (the latter shown in the two middle columns).
Notes | Pin | ![]() |
Pin | Notes | |||
---|---|---|---|---|---|---|---|
NC | 1 | AN | PWM | 16 | I1 | INT OUT 2 | |
NC | 2 | RST | INT | 15 | I2 | INT OUT 2 | |
SPI Chip Select | CS | 3 | CS | RX | 14 | NC | |
SPI Clock | SCK | 4 | SCK | TX | 13 | NC | |
SPI Data OUT | SDO | 5 | MISO | SCL | 12 | SCL | I2C Clock |
SPI Data IN | SDI | 6 | MOSI | SDA | 11 | SDA | I2C Data |
Power Supply | 3.3V | 7 | 3.3V | 5V | 10 | NC | |
Ground | GND | 8 | GND | GND | 9 | GND | Ground |
ONBOARD SETTINGS AND INDICATORS
Label | Name | Default | Description |
---|---|---|---|
LD1 | PWR | - | Power LED Indicator |
JP1,JP2,JP4 | COMM SEL | Right | Communication interface selection: right position SPI, left position I2C |
JP3 | ADDR SEL | Left | I2C address LSB selection: left position 0, right position 1 |
ACCEL 13 Click Board™ ELECTRICAL SPECIFICATIONS
Description | Min | Typ | Max | Unit |
---|---|---|---|---|
Receiver inputs voltage range | ±2 | - | ±16 | g |
Output refresh rate | 1.6 | - | 1600 | Hz |
Thermal measurement range | -40 | - | +85 | ˚C |
Frequently Asked Questions
Have a Question?
Be the first to ask a question about this.