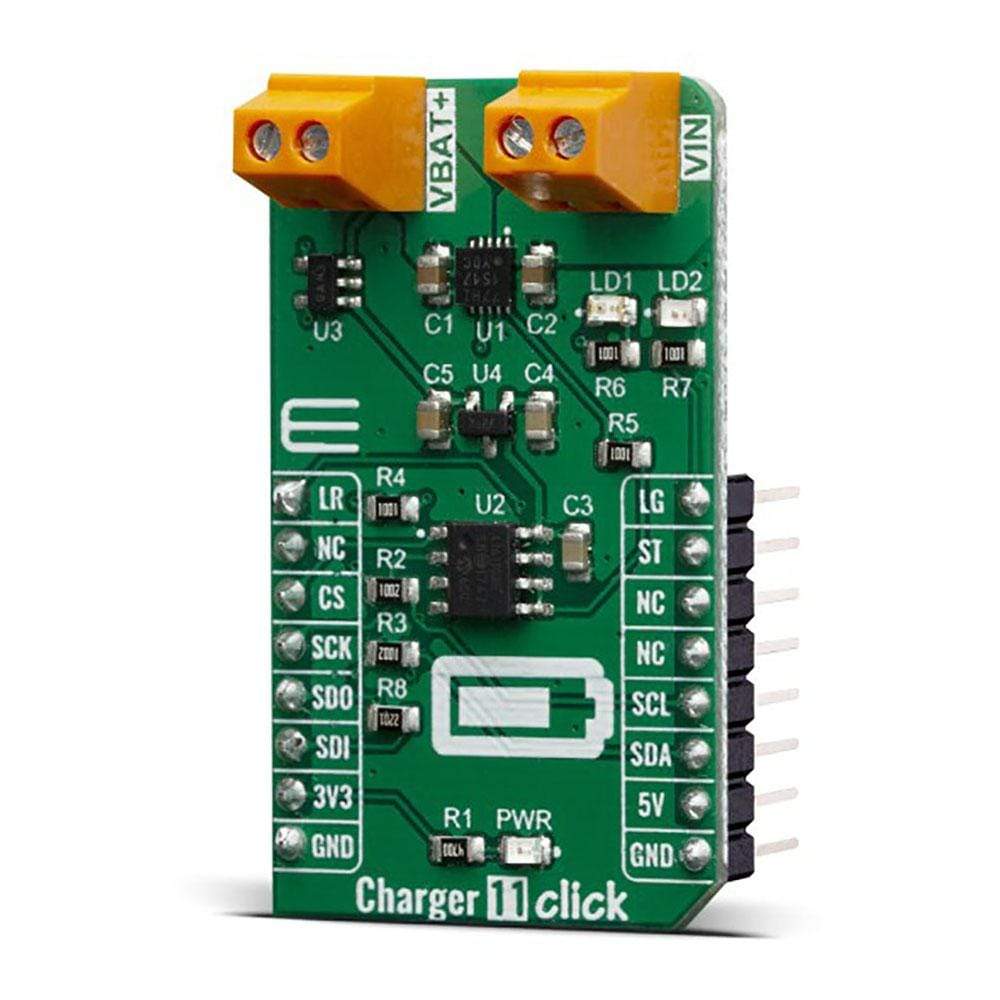
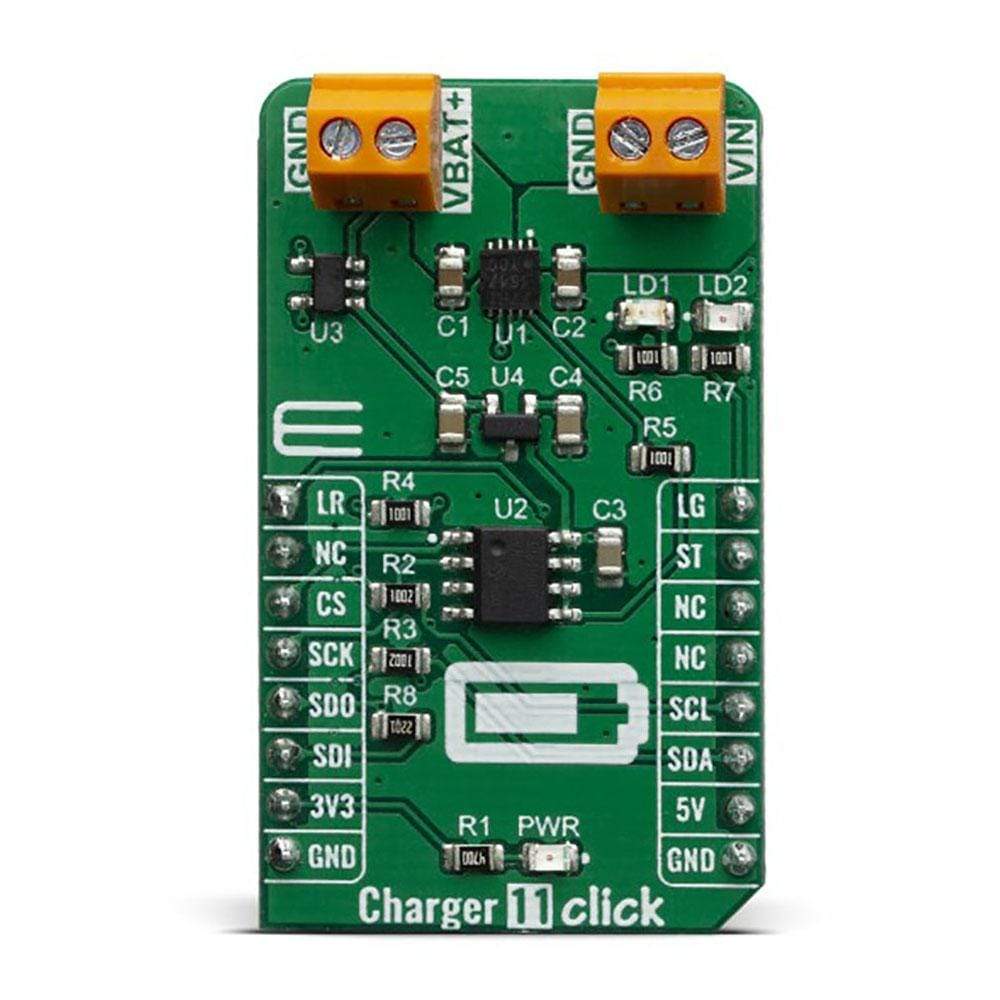
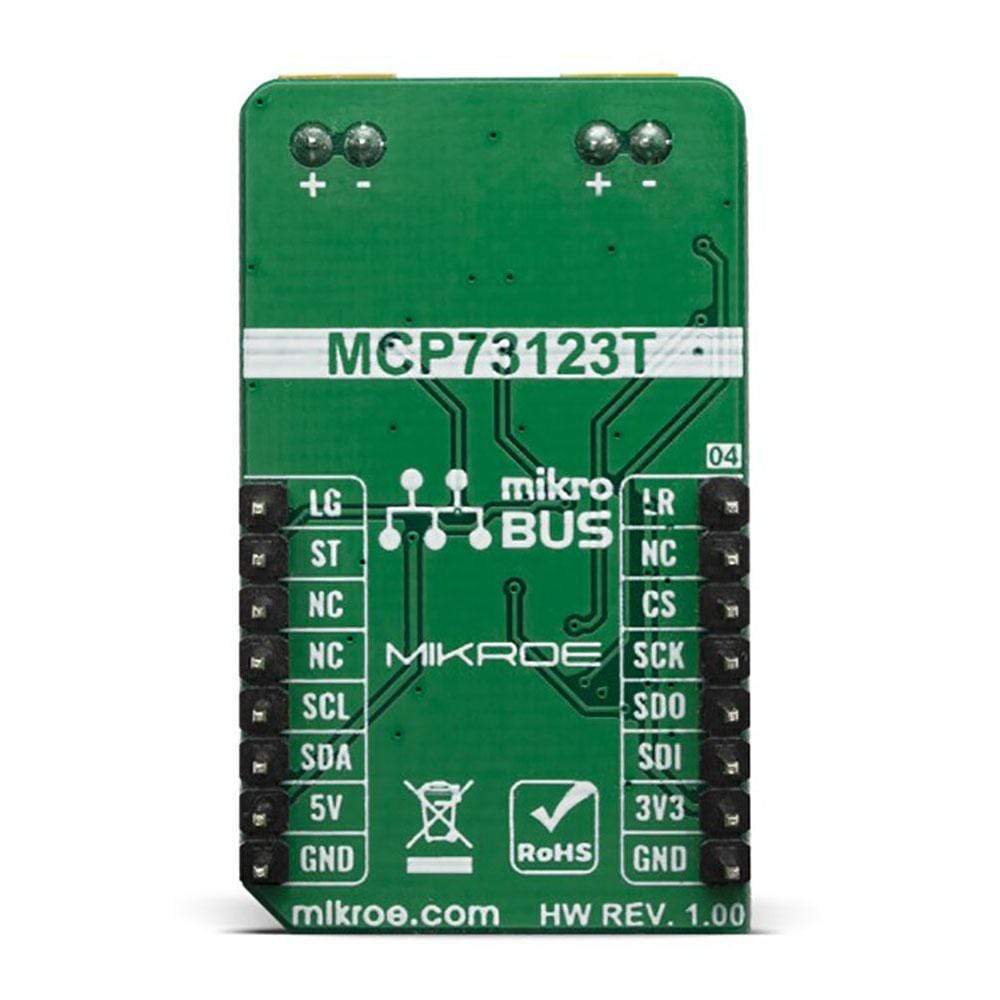
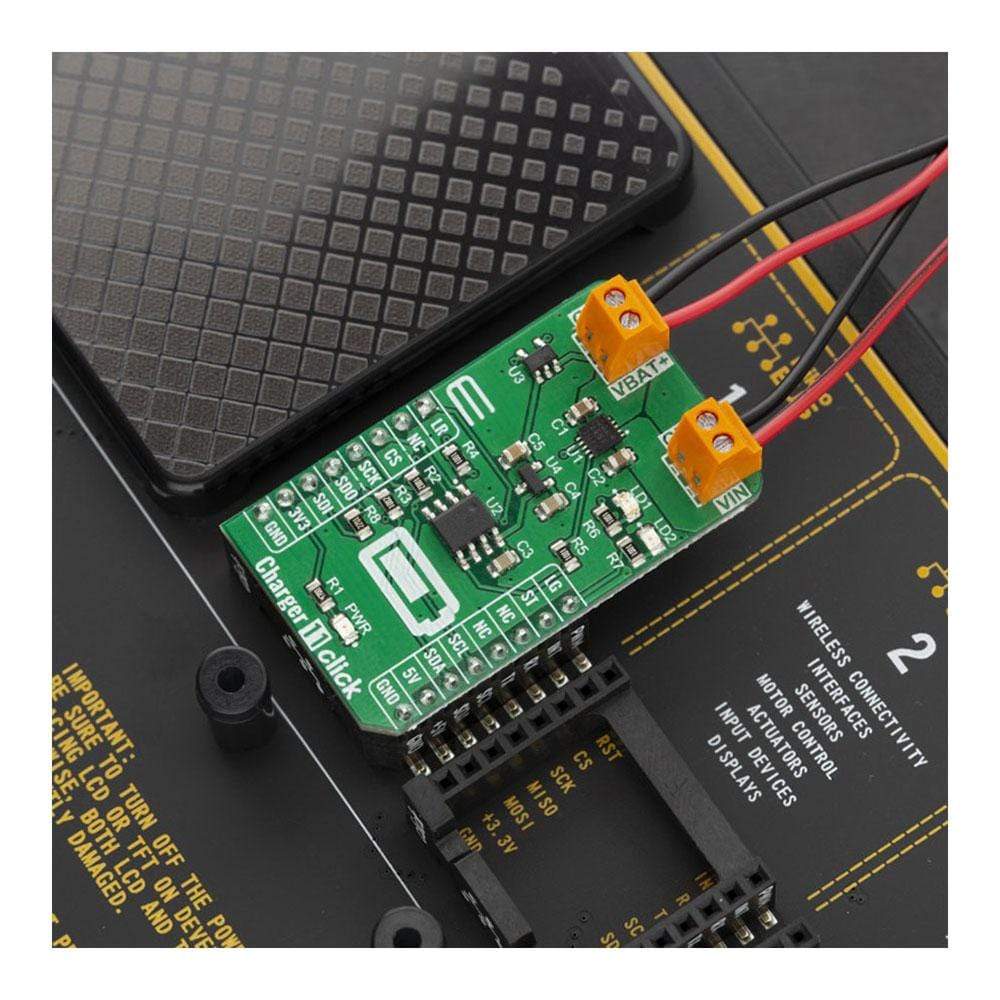
Overview
Das Charger 11 Click Board™ ist ein LiFePO4-Akkuladegerät (Lithium-Eisenphosphat). Dieses Click Board™ kann für kostengünstige LiFePO4-Akkuladegeräte oder Elektrowerkzeuge, Spielzeuge, Backup-Energiespeicherlösungen usw. verwendet werden. Das Charger 11 Click Board™ basiert auf dem MCP73123T-Controller, der über einige zusätzliche Funktionen verfügt, die ein Laden ohne allzu großen Aufwand ermöglichen.
Das Charger 11 Click Board™ verfügt über eine Ladestromregelung, die eine SPI-Schnittstelle über MCP4161 IC verwendet, ein 8-Bit-Digitalpotentiometer. Zur Überwachung der Batteriespannung verwendet diese Click Board™-Platine den Analog-Digital-Wandler MCP3221A5T über die I2C-Schnittstelle. Auf der Platine befinden sich eine Power-LED und zwei zusätzliche LEDs, die für Ladeanzeigen verwendet werden können.
General Information | |
---|---|
Part Number (SKU) |
MIKROE-3650
|
Manufacturer |
|
Physical and Mechanical | |
Weight |
0.021 kg
|
Other | |
Country of Origin |
|
HS Code Customs Tariff code
|
|
EAN |
8606018716371
|
Warranty |
|
As a Lithium Iron Phosphate battery requires a very accurate current and voltage for charging, Charger 11 click can be a perfect solution for such a task. The Charger 11 Click Board™ is equipped with a highly integrated LiFePO4 battery charger. This click has a charging current control IC over the SPI interface which ensures perfect and efficient charging. With Analog-To-Digital Converter through its 12-bit resolution and I2C interface, Charger 11 click has precise battery voltage monitoring. Charger 11 click meets all requirements for charging this higher specific capacity, but low-density batteries.
How Does The Charger 11 Click Board™ Work?
The Charger 11 Click Board™ is based on the MCP73123 - a highly integrated Lithium Iron Phosphate (LiFePO4) battery charge management controller for use in space-limited and cost-sensitive applications, from Microchip. MCP73123 is an efficient Lithium Iron Phosphate battery charger, thanks to specific charge algorithms for LiFePO4 batteries to achieve optimal capacity and safety in the shortest charging time possible. Along with its small physical size, the low number of external components makes this IC ideally suitable for various applications. MCP73123 is designed to employ a constant current and constant voltage charge algorithm. The 3.6V factory preset reference voltage simplifies the design. The fast charge constant current is set by a digital potentiometer, on this Click, it is MCP4161 with an external 1K resistor in series. The MCP73123 also limits the charge current based on the temperature during high power or high ambient conditions. This thermal regulation optimizes the charge cycle time while maintaining device reliability. PROG pin of the MCP73123 also serves as the enable pin, where on this Click it is wired in rheostat configuration with the digital potentiometer. That way the charging current can be controlled.
The digital potentiometer on Charger 11 Click Board™ is MCP4161 which offers a wide range of product offerings using an SPI interface. WiperLock technology allows application-specific calibration settings to be secured in EEPROM. This digital pot is tied with charger IC over its P0A control pin. By assigning values on MCP4161 from 0 to 10 kiloohms battery charging can be controlled. As there is a 1 K resistor in series it can never be 0 ohms on MCP73123 chargers PROG pin. However, maximum resistance cannot exceed 11 kiloohms. Fast charging can be regulated with 10K on PROG pin to get 130 mA. To get 1000 mA digital potentiometer needs to go down to 0,1 K, along with an external resistor, which makes 1,1 K. Communication with a digital potentiometer on this Click and that way controlling the charger is done through SPI interface.
Another feature of the Charger 11 Click Board is battery voltage monitoring which is done by using an MCP3221A5T Analog-To-Digital converter. It is a 12-bit resolution SOT12 package device which provides one single-ended input and is based on advanced CMOS technology. Communication to the MCP3221A5T is done by the I2C interface where standard and fast modes are available for this device.
The Charger 11 Click Board™ for voltage reference use an MCP1541, which has a high precision output voltage of 4.096 volts, and which is then compared to battery voltage in order to get precise measurements. This voltage reference circuit uses a combination of an advanced CMOS design and EPROM timing to provide initial tolerance of ±1% max.
On the right side of the click board is an input screw terminal with corresponding markings, where the recommended external voltage of 6V can be applied. The left screw terminal is reserved for a Lithium Iron Phosphate battery with GND and VBAT+ markings. When connected to a power source, the green PWR LED will indicate it. Red LED1 and green LED2 can be used for visual charge monitoring. As those two LEDs are multipurpose, they can be used for various things.
Specifications
Type | Battery charger |
Applications | The Charger 11 Click Board™ is a perfect choice for the development of LiFePO4 battery charging applications. It offers two screw terminal connections, LED indicators for fast and easy prototyping. |
On-board modules | MCP73123, a highly integrated Lithium Iron Phosphate LiFePO4 battery charge management controller. |
Key Features | Designed for safe and efficient charging one LiFePO4 battery, battery voltage monitoring, two screw terminals, two multipurpose indicators over LEDs and mikroBUS™ pins, etc. |
Interface | GPIO,I2C,SPI |
Compatibility | mikroBUS |
Click board size | M (42.9 x 25.4 mm) |
Input Voltage | 3.3V,5V |
Pinout Diagram
This table shows how the pinout on the Charger 11 Click Board™ corresponds to the pinout of the mikroBUS™ socket (the latter shown in the two middle columns).
Notes | Pin | ![]() |
Pin | Notes | |||
---|---|---|---|---|---|---|---|
Red LED Indicator | LR | 1 | AN | PWM | 16 | LG | Green LED Indicator |
NC | 2 | RST | INT | 15 | ST | Status Out | |
Chip Select | CS | 3 | CS | RX | 14 | NC | |
Serial Clock | SCK | 4 | SCK | TX | 13 | NC | |
Serial data out | SDO | 5 | MISO | SCL | 12 | SCL | I2C Clock |
Serial data in | SDI | 6 | MOSI | SDA | 11 | SDA | I2C Data |
Power Supply | 3.3V | 7 | 3.3V | 5V | 10 | 5V | Power Supply |
Ground | GND | 8 | GND | GND | 9 | GND | Ground |
Frequently Asked Questions
Have a Question?
Be the first to ask a question about this.