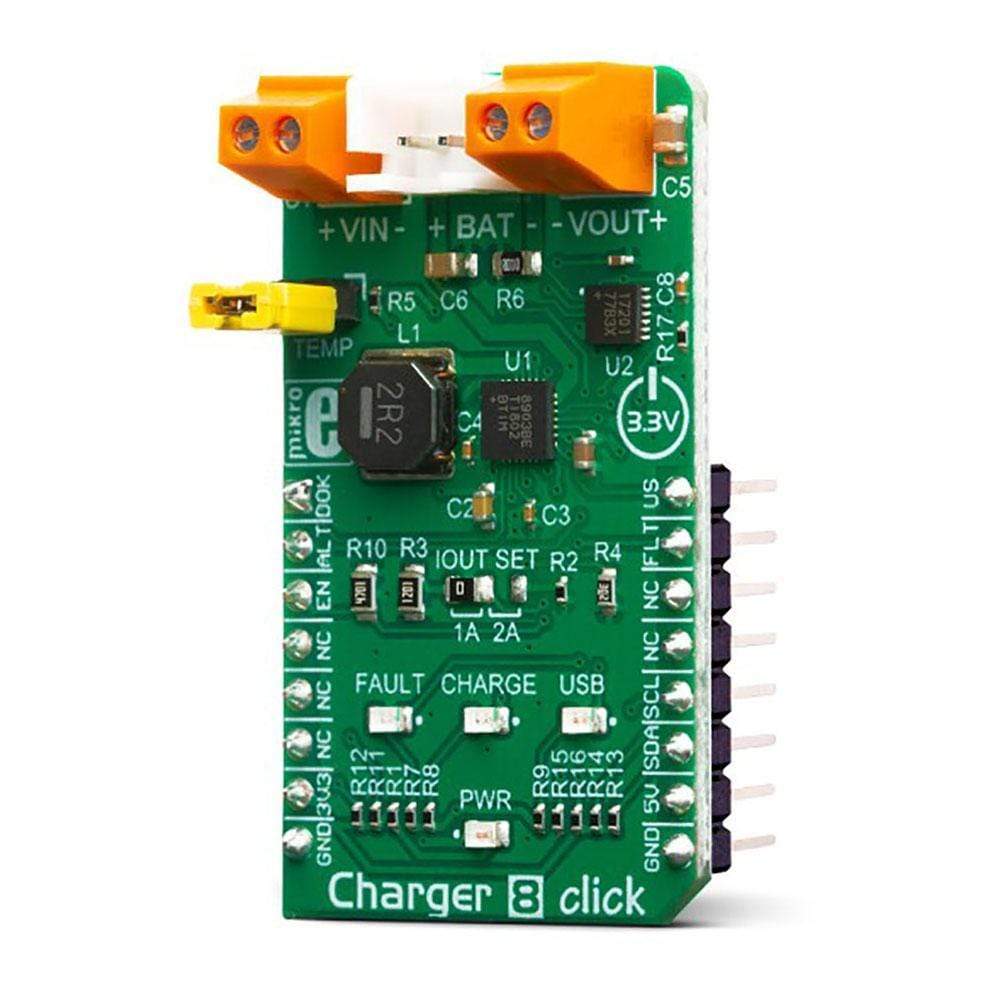
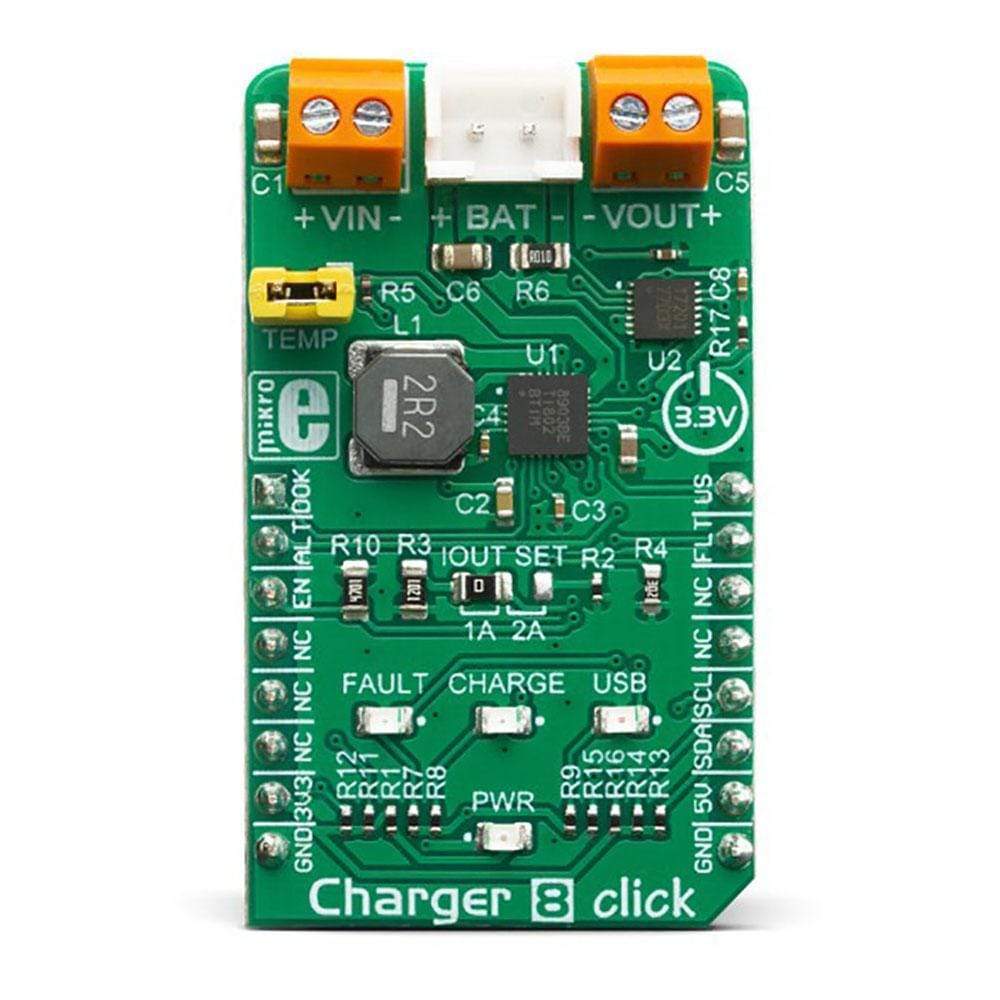
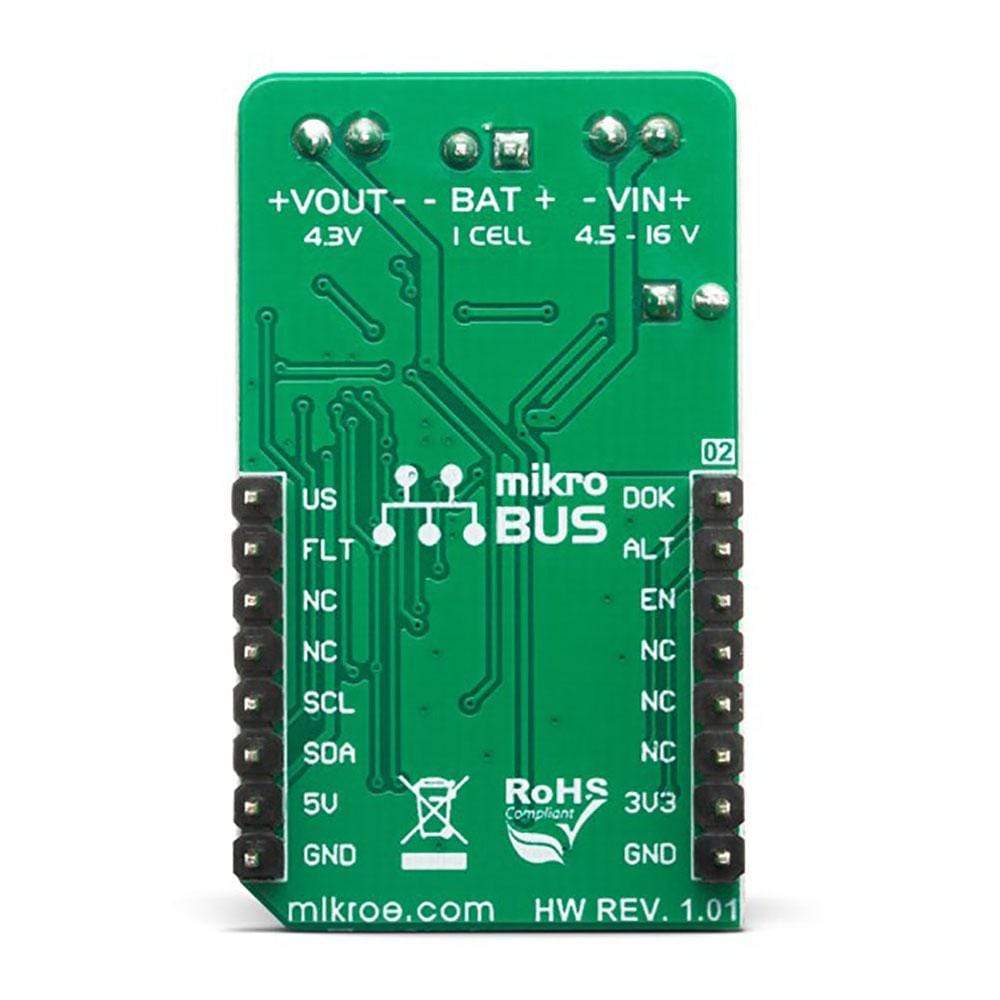
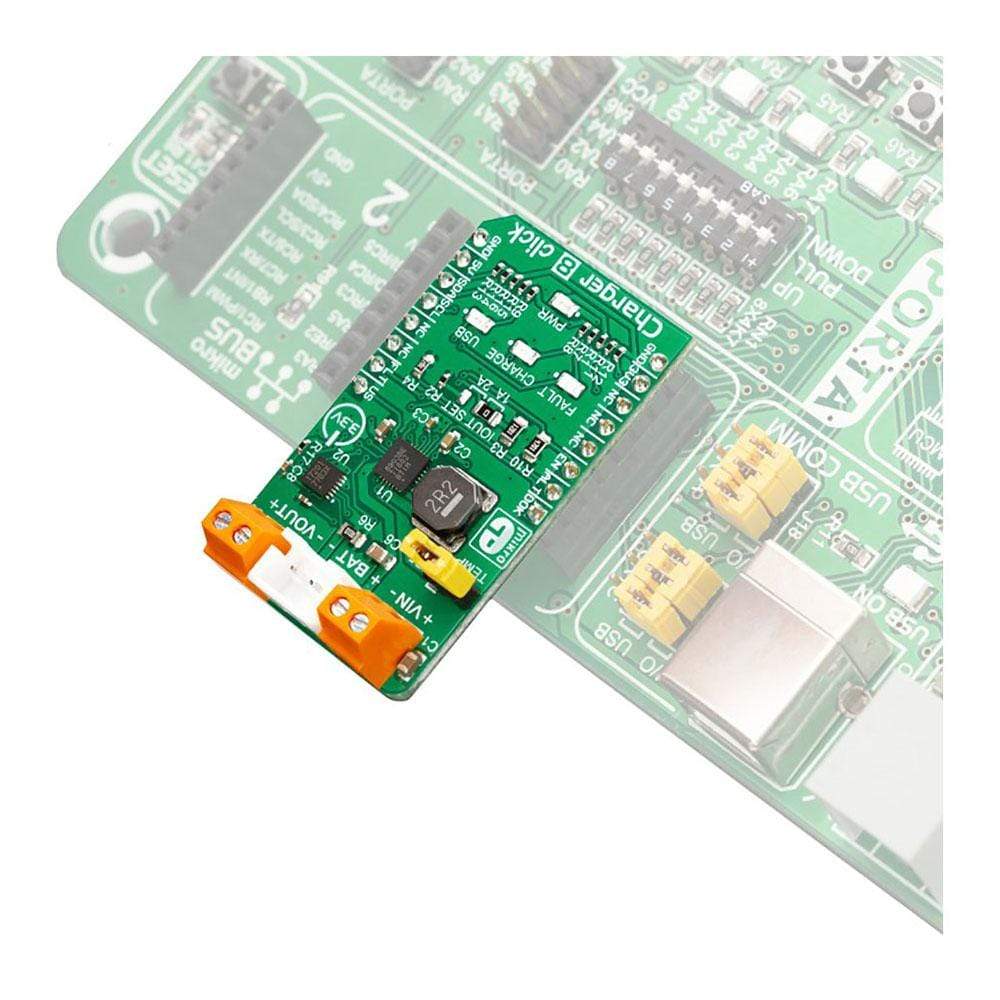
Overview
Das Charger 8 Click Board™ ist ein intelligentes Li-Ion-Akkuladegerät, System-Power-Manager und Akku-Ladestandsanzeige-Click Board™. Als System-Stromverteiler kann es bis zu 2 A an eine angeschlossene Last liefern. Durch Verwendung eines extern angeschlossenen Netzteils kann es einen einzelligen Li-Po/Li-Ion-Akku laden. Ein dedizierter Power-Management-IC mit der optimierten intelligenten Stromsteuerung ermöglicht eine sehr effiziente Verwaltung der verfügbaren Leistung.
Ein zusätzlicher IC zur Batterie-Ladezustandsanzeige mit einem proprietären Algorithmus zur Vorhersage der Batteriealterung und einer Schätzung der Zeit bis zum Entleeren/Volltanken bietet eine vollständige Diagnose im Zusammenhang mit dem Ladevorgang der Batterie.
General Information | |
---|---|
Part Number (SKU) |
MIKROE-3348
|
Manufacturer |
|
Physical and Mechanical | |
Weight |
0.02 kg
|
Other | |
Country of Origin |
|
HS Code Customs Tariff code
|
|
EAN |
8606018714452
|
Warranty |
|
Equipped with the intelligent power management and battery fuel gauge ICs, the Charger 8 Click Board™ is the complete power solution for many embedded and consumer applications that rely on the efficient power ORing and an advanced battery charging functionality. The Charger 8 Click Board™ can be used as a part of the power supply and distribution system in many applications: different kinds of handheld appliances, portable media players, portable audio players, and other general-purpose battery-operated electronic devices.
How Does The Charger 8 Click Board™ Work?
The Charger 8 Click Board™ is based on two different ICs: It uses the MAX8903B, an integrated single cell Li-Ion/Li-Po battery charger for USB and external power, as well as the MAX17201, a stand-alone battery fuel gauge with SHA-256 authentication, both ICs from Maxim Integrated.
The MAX8903B is labeled as U1, and it provides the majority of functions for the Charger 8 Click Board™. Its basic task is to provide power for the system load and charge a single-cell Li-Ion/Li-Po battery, connected at the standard 2.5mm pitch XS battery connector, labeled as BAT. When the USB input is used as a primary power source, the MAX8903B will try to maintain the system current by utilizing the connected battery or the external power supply unit (PSU) at the VIN input. On the other hand, it will try to redirect all the unused power to the battery charging section in cases when the system requires lower current levels. With the help of the Smart Power Selector™ technology, it will always choose the best path in order to utilize the limited power resources in the most efficient way.
The MAX8903B IC is designed with reliability in mind: the IC prevents draining the battery below the critical level, protects it from overheating (if thermistor is used), offers prequel charging (for deeply depleted batteries), features an overvoltage protection, charging status monitoring and so on. The Click board™ itself is equipped with a set of indicators used to monitor both charging process and power distribution.
- USB LED indicates that there is a valid voltage at the USB input. Instead to the USB connector, the USB power supply input pin of the MAX8903B is connected to the mikroBUS™ 5V power rail.
- CHARGE LED indicates the charge-in-progress status.
- FAULT LED indicates an error during charging process.
Besides the FAULT LED indicator, the FAULT pin of the MAX8903B is also routed to the mikroBUS™ INT pin, allowing an interrupt to be generated on the host MCU in case of a charging failure. This pin will be pulled to a LOW logic level when the charging timer expires while the charger is still in prequel mode (mode in which only 10% of charging current is applied to the battery, while it is deeply discharged), or while the battery stays in fast-charging mode.
DOK pin is routed to the mikroBUS™ AN pin, labeled as DOK. A logic LOW level on this pin indicates that there is a valid power supply at the DC power supply input pin of the MAX8903B. If there is a PSU connected to the VIN terminal, its voltage should stay within the valid range. The undervoltage/overvoltage protection will be activated if the internal voltage threshold is exceeded. The absolute maximum voltage rating of the MAX8903B is 20V.
USB Suspend (USUS) pin from the MAX8903B is routed to the mikroBUS™ PWM pin, and it is labeled as US. It is used to suspend the power source connected to the USB power supply input pin. With no external PSU connected, setting this pin to a HIGH logic level will disable the battery charger and the SYS output, allowing the USB SUSPEND mode.
The CEN pin is used to disable the charging circuitry. It is pulled to a LOW logic level by a resistor, and the MAX8903B should be controlling this pin internally for optimum performance. However, if battery charging is not wanted, it can be forced off by pulling this pin to a HIGH logic level. It is routed to the mikroBUS™ pin CS and labeled as EN.
The MAX17201 IC offers a battery gauge functionality, allowing to monitor the performance of the connected battery. It employs a proprietary ModelGauge™ m5 algorithm, which allows very accurate monitoring of all battery parameter, including the predicted aging time, remaining cycles and so on. It has a programmable ALERT function which is signaled over the ALTR1 pin, routed to the mikroBUS™ RST pin, labeled as ALT. The MAX17201 IC uses the I2C interface to communicate with the host MCU.
SPECIFICATIONS
Type | Battery charger |
Applications | The Charger 8 Click Board™ can be used as a part of the power supply and distribution system in many applications: different kinds of handheld appliances, portable media players, portable audio players, and other general-purpose battery-operated electronic devices. |
On-board modules | MAX8903B, an integrated single cell Li-Ion/Li-Po battery charger for USB and external power; MAX17201, a stand-alone battery fuel gauge with SHA-256 authentication, both ICs from Maxim Integrated. |
Key Features | The Charger 8 Click Board™ is designed for a safe and efficient charging of Li-Po / Li-ion batteries, and optimized power management and distribution. Dedicated battery fuel gauge IC with advanced measurement and prediction algorithms. Selectable charging current up to 2A. |
Interface | GPIO,I2C |
Compatibility | mikroBUS |
Click board size | M (42.9 x 25.4 mm) |
Input Voltage | 3.3V,5V |
PINOUT DIAGRAM
This table shows how the pinout on the Charger 8 Click Board™ corresponds to the pinout on the mikroBUS™ socket (the latter shown in the two middle columns).
Notes | Pin | ![]() |
Pin | Notes | |||
---|---|---|---|---|---|---|---|
External PSU OK | DOK | 1 | AN | PWM | 16 | US | USB Suspend |
Battery Gauge Alert | ALT | 2 | RST | INT | 15 | FLT | Fault Indicator |
Charger Enable | EN | 3 | CS | RX | 14 | NC | |
NC | 4 | SCK | TX | 13 | NC | ||
NC | 5 | MISO | SCL | 12 | SCL | I2C Clock | |
NC | 6 | MOSI | SDA | 11 | SDA | I2C Data | |
Power Supply | 3.3V | 7 | 3.3V | 5V | 10 | 5V | Power Supply |
Ground | GND | 8 | GND | GND | 9 | GND | Ground |
CHARGER 8 CLICK ELECTRICAL SPECIFICATIONS
Description | Min | Typ | Max | Unit |
---|---|---|---|---|
Input Voltage (at VIN terminal) | 4.6 | 5 | 16 | V |
System output voltage (at VOUT terminal) | 4.265 | 4.395 | V | |
Charging Current (max current selectable by IOUT SEL) | 0.5 | 1 (2) | A |
ONBOARD SETTINGS AND INDICATORS
Label | Name | Default | Description |
---|---|---|---|
LD1 | PWR | - | Power LED indicator |
LD2 | FAULT | - | Charger fault LED indicator |
LD3 | CHARGE | - | Charger status LED indicator |
TB1 | VOUT | - | System power supply output |
TB2 | VIN | - | External PSU input connector |
J1 | BAT | - | 2.5mm pitch standard battery XS connector |
J2 | TEMP | - | Optional battery thermistor connector (should be shorted if not used) |
JP1 | IOUT SEL | Left | Current limit selection for the battery charger: left position 1A, right position 2A |
Frequently Asked Questions
Have a Question?
Be the first to ask a question about this.