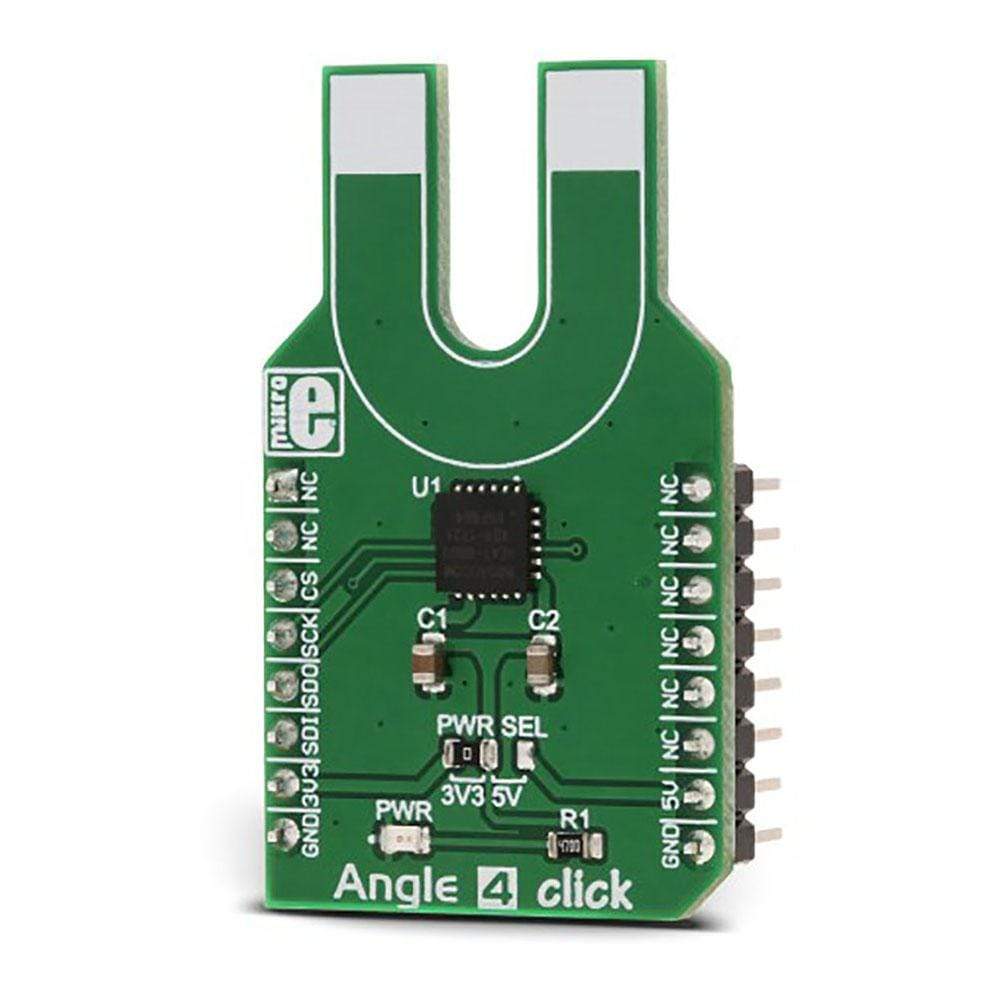
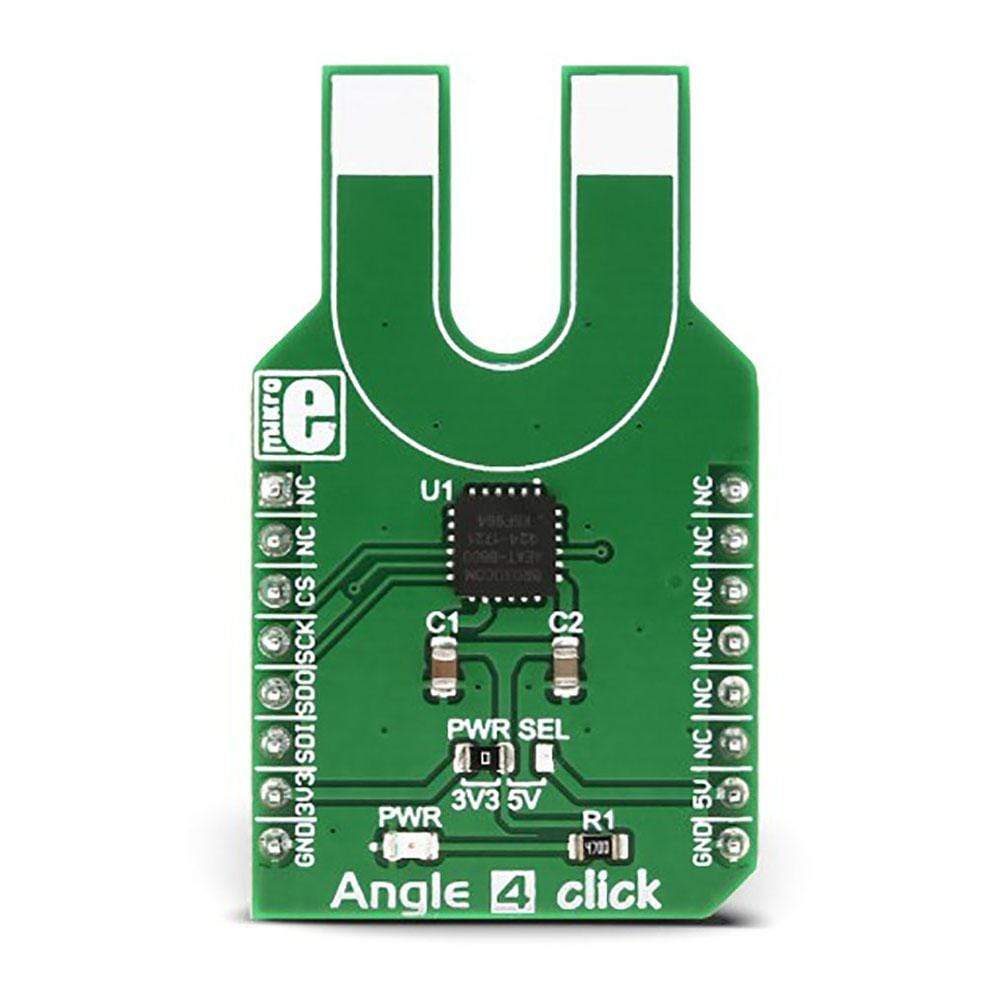
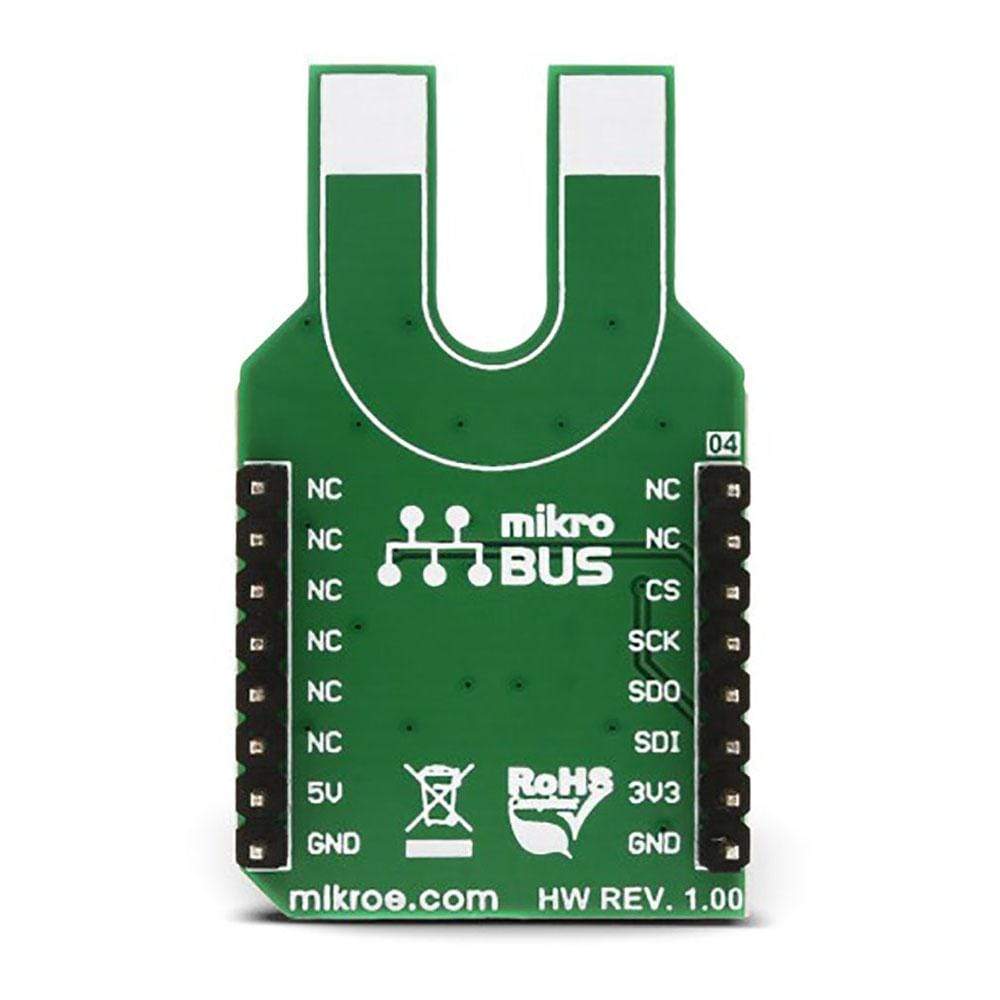
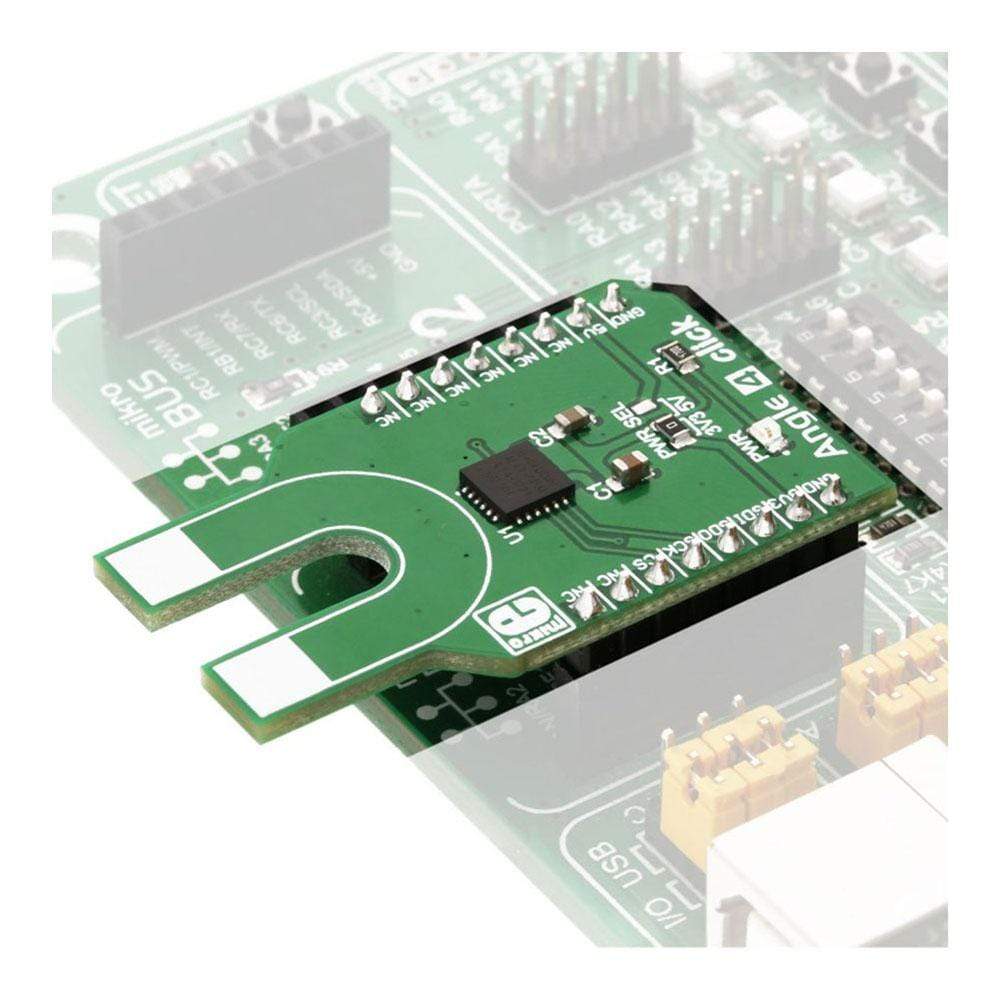
Overview
Das Angle 4 Click Board™ ist ein magnetischer Winkelsensor, der als Drehgeber verwendet werden kann. Mithilfe des AEAT-8800-Q24, einem integrierten programmierbaren 10- bis 16-Bit-Winkelmagnetgeber, kann das Angle 4 Click Board™ die Magnetfeldrotation über den gesamten Bereich von 360° erfassen, die auf die Mitte des Sensors ausgerichtet ist. Die absolute Winkelposition kann über die SPI-Schnittstelle gelesen werden.
Der Sensor-IC selbst bietet eine vielseitige berührungslose Rotationssensorplattform mit der Möglichkeit, mehrere wichtige Arbeitsparameter wie Auflösung, Nullposition, Richtung, Hysterese und mehr fein abzustimmen.
General Information | |
---|---|
Part Number (SKU) |
MIKROE-3130
|
Manufacturer |
|
Physical and Mechanical | |
Weight |
0.019 kg
|
Other | |
Country of Origin |
|
HS Code Customs Tariff code
|
|
EAN |
8606018713424
|
Warranty |
|
The AEAT-8800-Q24 IC utilizes integrated Hall sensor elements, accompanied by very sophisticated circuits for processing analog and digital signals, resulting in a very robust and precise rotary sensing interface. This makes Angle 4 Click Board™ an ideal solution for a wide variety of contactless angle measurement applications, such as the acquisition of position and rotation for various BLDC or stepper motors, mechanical potentiometer replacement, for building various HMI platforms, in robotics, and similar applications.
How Does The Angle 4 Click Board™ Work?
As already mentioned, Angle 4 Click Board™ uses the AEAT-8800-Q24, an integrated 10 to 16-bit programmable angular magnetic encoder, by Broadcom. This sensor relies on integrated Hall elements and complex analog front end and digital signal processing, in order to provide absolute angular position over the industry standard SPI interface. The user has the ability to programmatically set the zero position, direction, hysteresis, and the resolution. This allows the Click Board™ to be tailored according to needs for a range of different applications.
The possibility to sense the rotational angle of a diametrically magnetized object parallel with the Click Board™ surface, gives an opportunity to develop both contactless rotational and positional measurement applications, as well as the human-machine interfaces (HMI), such as the rotary encoders, digital potentiometers, and similar. The calibration is simple, and the AEAT-8800-Q24 datasheet provides a detailed explanation how to calibrate the device by using a diametrically magnetized object (i.e. a magnetic disc), with its axis aligned to the center of the sensor. For the best results, the magnet properties should be according to specifications in the datasheet. Once calibrated, it can be permanently used, with no additional recalibrations.
The AEAT-8800-Q24 uses the non-volatile one-time programming memory during the operation. It contains registers with the calibration values, zero offsets, resolution and so on. All the OTP locations have their shadow locations, which allow writing, but only when the unlock command is issued (writing 0xAB to the location 0x10). However, the values will be lost after the power cycle and will be rewritten with the values contained in the OTP memory.
The library provided with Angle 4 Click Board™ offers several simple and useful functions, among which is the angle4_calibration function, which will automatically program the direction and the resolution parameters to the OTP memory, passed as argumetns to this function. However, the OTP memory will not be permanently written, unless appropriate programming voltage is applied to the VDDP pin. Since the OTP memory can be programmed only once, a thorough understanding of the OTP programming process is required. More information about the OTP programming process can be found in the AEAT-8800-Q24 datasheet.
The Angle 4 Click Board™ contains an SMD jumper, labelled as PWR SEL, which can be used to set the operating voltage of the Click Board™ to either 3.3V or to 5V. This allows a wide range of different MCUs to be interfaced with the Click Board™, operating both at 3.3V and 5V.
SPECIFICATIONS
Type | Magnetic |
Applications | It is an ideal solution for a wide variety of contactless angle measurement applications, such as the acquisition of position and rotation for various BLDC or stepper motors, mechanical potentiometer replacement, for building various HMI platforms, in robotics, and similar applications |
On-board modules | AEAT-800-Q24, an integrated 10 to 16-bit programmable angular magnetic encoder, by Broadcom |
Key Features | Accurate sensing of the magnetic angle, providing absolute positional readings over the SPI, good linearity and low error margin over 360, programmable working parameters, OTP memory for permanent working parameters storage |
Interface | SPI |
Compatibility | mikroBUS |
Click Board™ size | M (42.9 x 25.4 mm) |
Input Voltage | 3.3V or 5V |
PINOUT DIAGRAM
This table shows how the pinout on Angle 4 Click Board™ corresponds to the pinout on the mikroBUS socket (the latter shown in the two middle columns).
Notes | Pin | ![]() |
Pin | Notes | |||
---|---|---|---|---|---|---|---|
NC | 1 | AN | PWM | 16 | NC | ||
NC | 2 | RST | INT | 15 | NC | ||
SPI Chip Select | CS | 3 | CS | RX | 14 | NC | |
SPI Clock | SCK | 4 | SCK | TX | 13 | NC | |
SPI Data OUT | SDO | 5 | MISO | SCL | 12 | NC | |
SPI Data IN | SDI | 6 | MOSI | SDA | 11 | NC | |
Power supply | 3.3V | 7 | 3.3V | 5V | 10 | 5V | Power supply |
Ground | GND | 8 | GND | GND | 9 | GND | Ground |
ONBOARD SETTINGS AND INDICATORS
Label | Name | Default | Description |
---|---|---|---|
LD1 | PWR | - | Power LED indicator |
JP1 | PWR SEL | Left | Power supply voltage selection: left position 3.3V, right position 5V |
Frequently Asked Questions
Have a Question?
Be the first to ask a question about this.