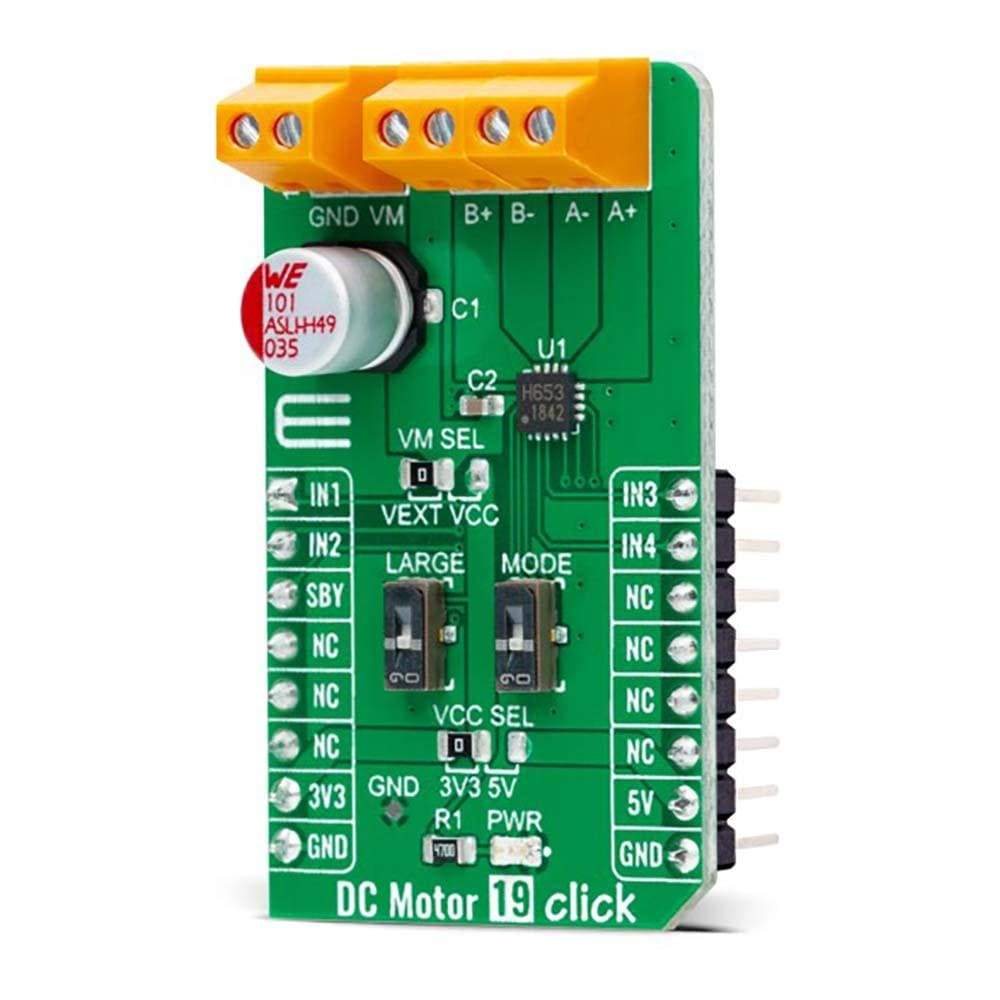
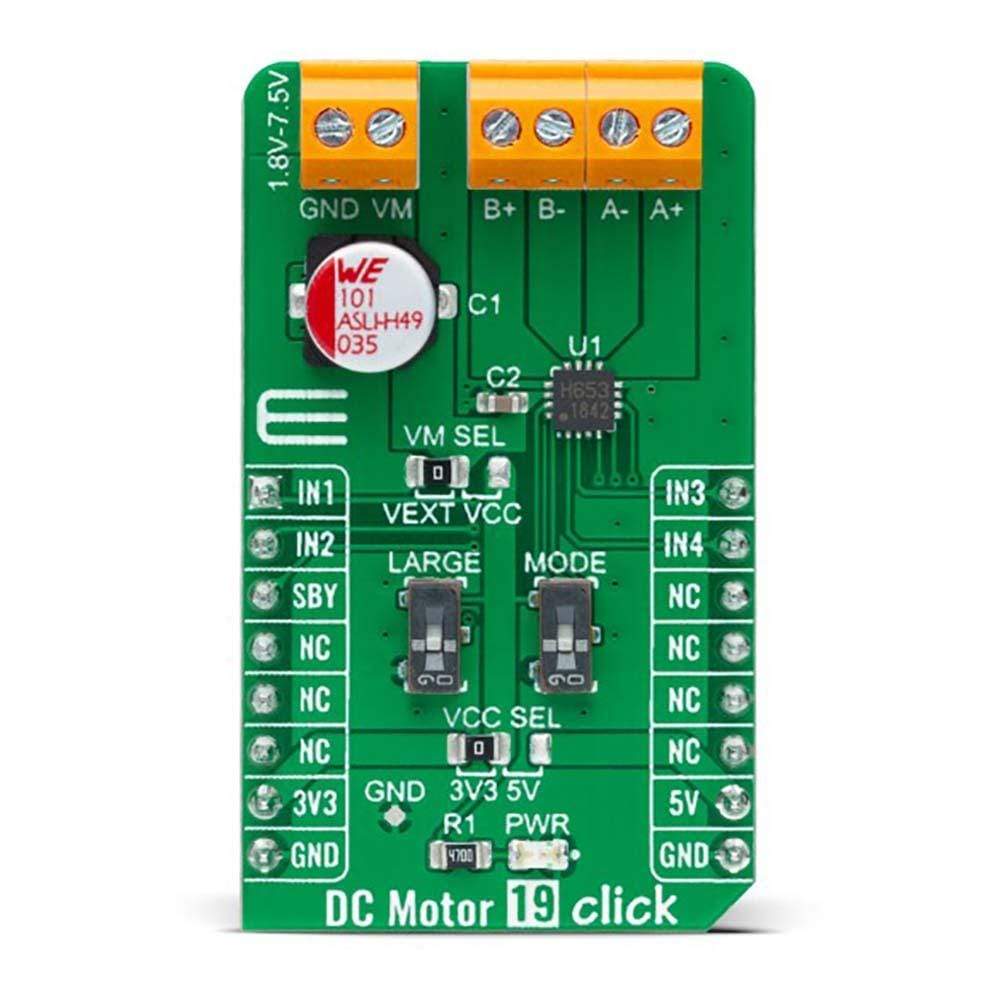
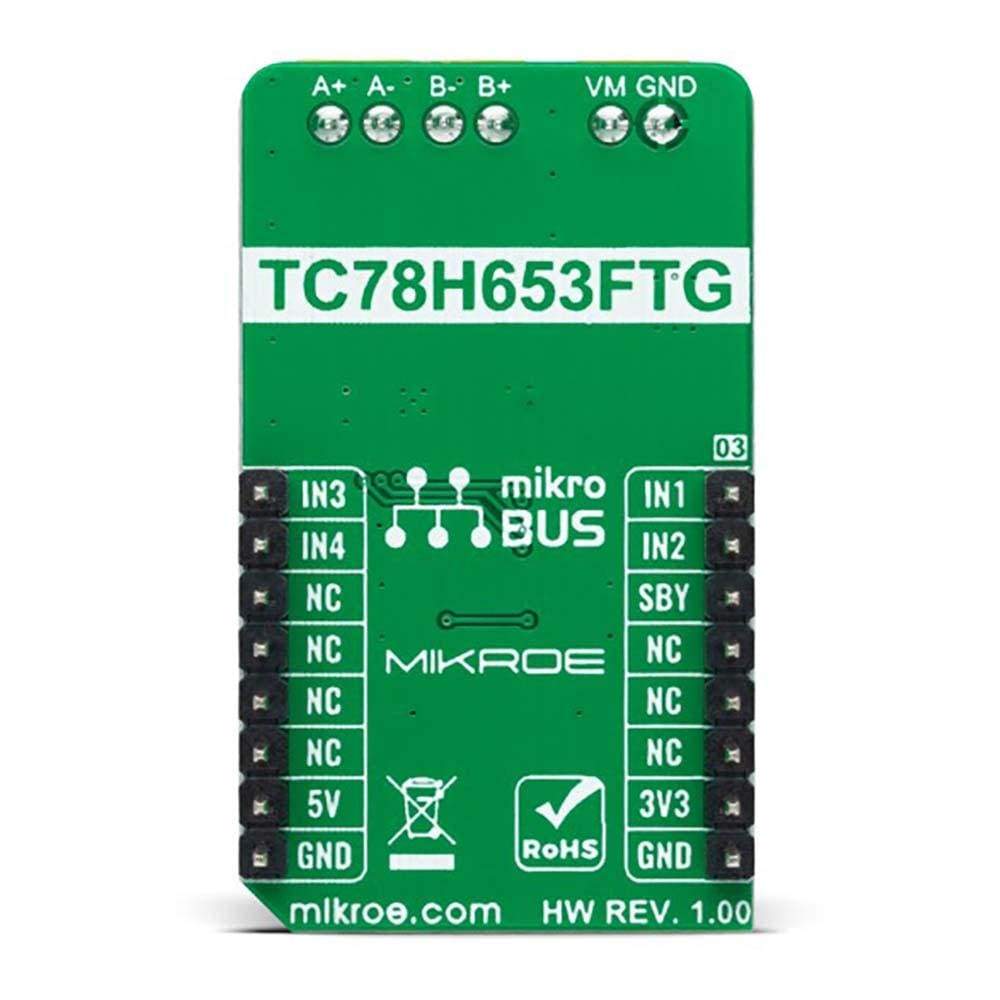

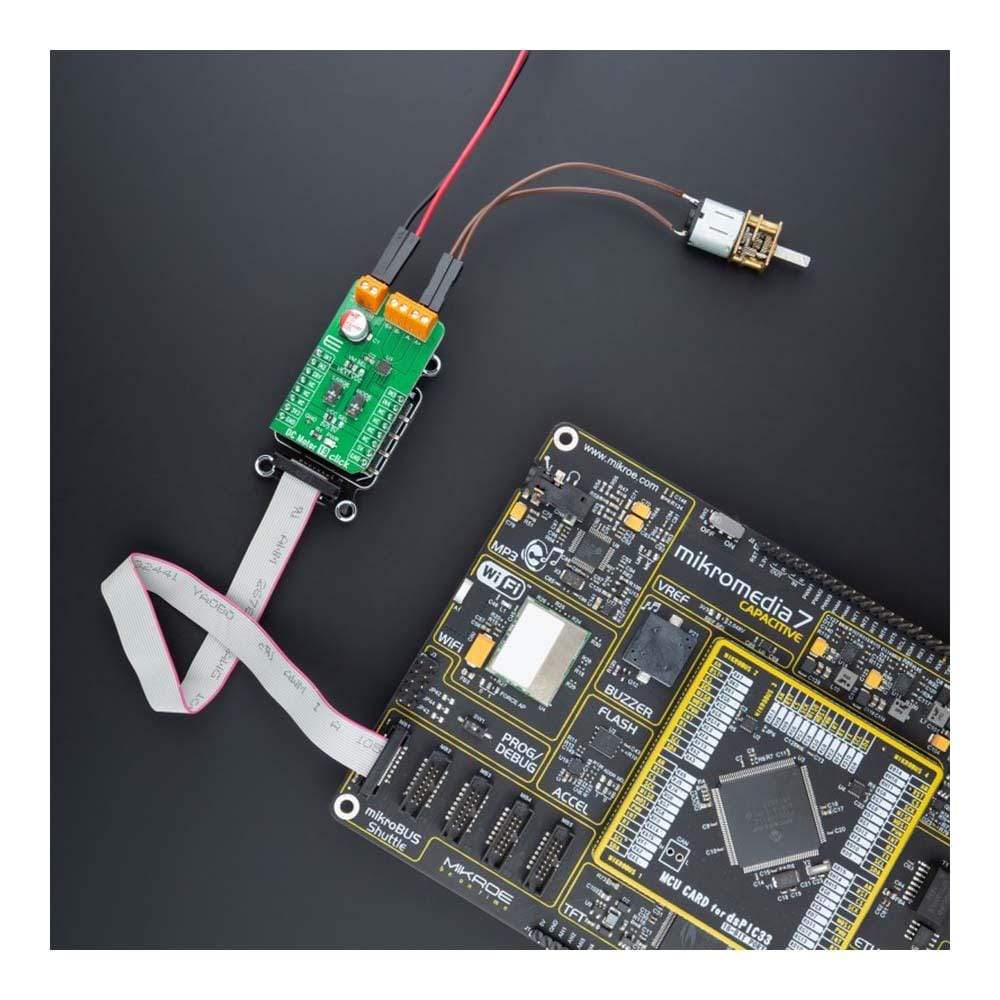
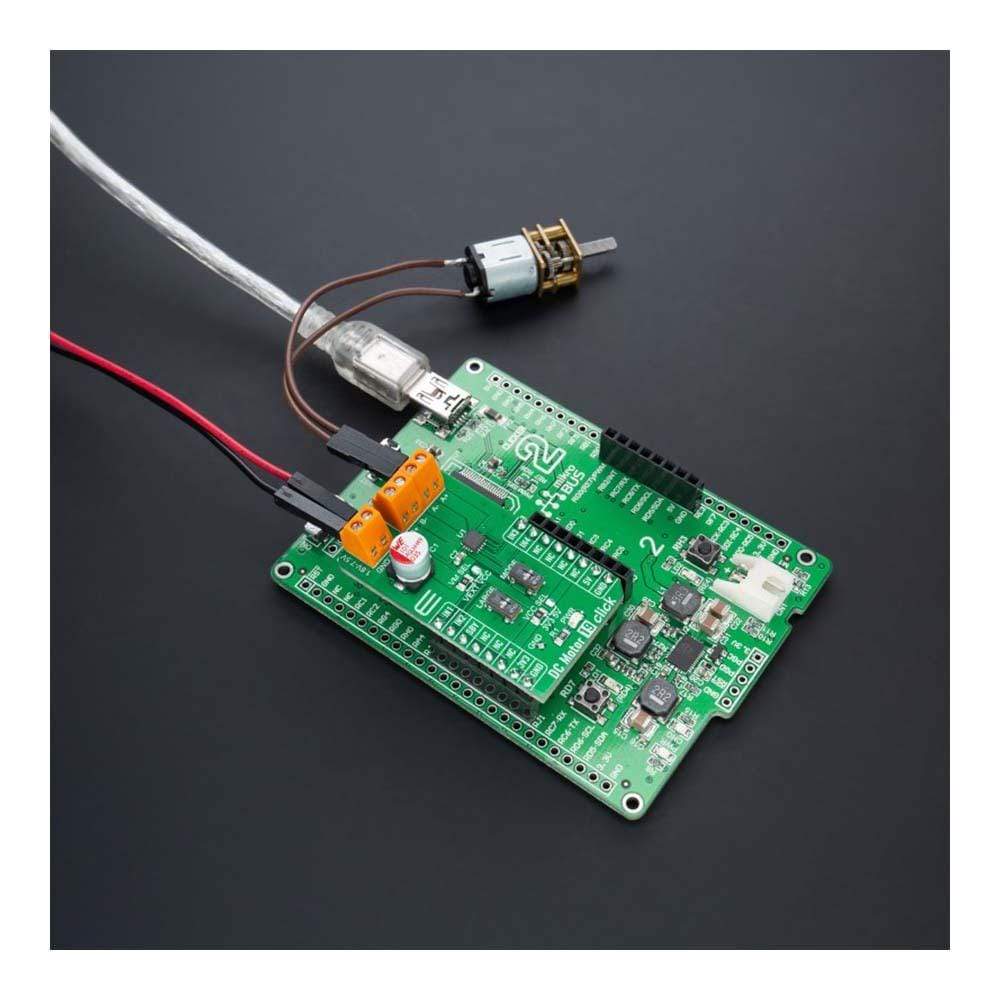
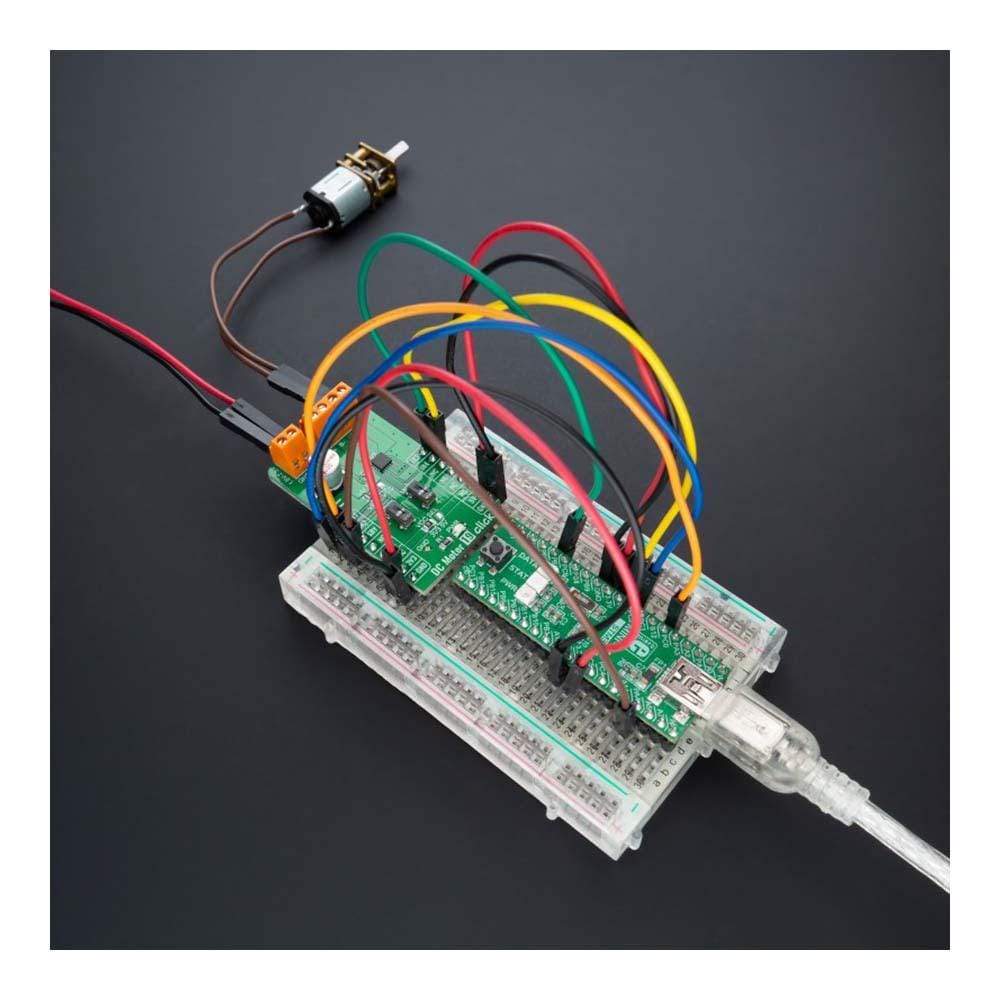
Overview
The DC Motor 19 Click Board™ is a compact add-on board that contains a brushed DC motor driver. This board features the TC78H653FTG, a dual H-bridge driver for one or two DC brushed motors or one stepping motor, which incorporates DMOS with low ON resistance in output transistors from Toshiba Semiconductor.
The Forward/Reverse/Brake/Stop mode can be selected according to the state of its input control signals, while the motor operation and current mode can be chosen through onboard switches alongside control signals. It has a wide operating voltage range of 1.8V to 7.5V with an output current capacity of 4A (DC). Besides, it also features built-in protection against under-voltage, overcurrent, and overtemperature conditions.
The DC Motor 19 Click Board™ is suitable for driving DC brushed motors and stepping motors for low voltage equipment such as home electronic products and devices using a 5V USB power supply.
General Information | |
---|---|
Part Number (SKU) |
MIKROE-4883
|
Manufacturer |
|
Physical and Mechanical | |
Weight |
0.02 kg
|
Other | |
Country of Origin |
|
HS Code Customs Tariff code
|
|
EAN |
8606027384042
|
Warranty |
|
How Does The DC Motor 19 Click Board™ Work?
The DC Motor 19 Click Board™ as its foundation uses the TC78H653FTG, a dual H-bridge driver for one or two DC brushed motors or one stepping motor from Toshiba Semiconductor. The integrated MOSFETs, which configures with an H-Bridge circuit inside the TC78H653FTG, use DMOS elements with low-on resistance (0.11Ω typical with 5V power supply and activated Large mode). It has a wide operating voltage range with an output current capacity of 4A (DC) and control functions, including motor-related functions (Forward, Reverse, Brake, Stop), current control, and built-in detection circuits for overcurrent, overheat, and low/high voltage.
As mentioned in the product description, the DC Motor 19 Click Board™ communicates with MCU using several GPIO pins. Also, this Click board™ has a Standby pin labeled as SBY routed to the CS pin of the mikroBUS™ socket used to switch to Standby mode by toggling the pin. When the SBY pin is low, TC78H653FTG stops supplying the power to the logic circuit, the Standby current is significantly reduced because all circuits in the IC are configured with CMOS/DMOS elements, and the current consumption in this mode is 0μA typical.
To turn ON the internal MOSFETs of the TC78H653FTG, they need to be switched by the logic level, which is input to the control input pins: IN1, IN2, IN3, and IN4 pins routed to the RST, AN, PWM, and INT pins of the mikroBUS™ socket. Thereby, the Forward/Reverse/Brake/Stop rotation direction mode can be selected according to the state of its input control signals, while the motor operation and current mode can be chosen through onboard switches labeled as MODE and LARGE, alongside control signals. With active LARGE mode, IN1 and IN2 pins control this mode while motor control pins A+ and A- are connected as OUT+ pin and pins B- and B+ pin are connected as OUT- pin. More information on the Motor Mode Selection can be found in the attached datasheet.
The DC Motor 19 Click Board™ supports an external power supply for the TC78H653FTG, which can be connected to the input terminal labeled as VM and should be within the range of 1.8V to 7.5V, while the DC motor coils can be connected to the terminals labeled as B+, B-, A-, and A+.
The DC Motor 19 Click Board™ can operate with both 3.3V and 5V logic voltage levels selected via the VCC SEL jumper. This way, it is allowed for both 3.3V and 5V capable MCUs to use communication lines properly. However, the Click board™ comes equipped with a library containing easy-to-use functions and an example code that can be used, as a reference, for further development.
SPECIFICATIONS
Type | Brushed |
Applications | Can be used for driving DC brushed motors and stepping motors for low voltage equipment such as home electronic products and devices using a 5V USB power supply |
On-board modules | TC78H653FTG - dual H-bridge driver for one or two DC brushed motors or one stepping motor from Toshiba Semiconductor |
Key Features | Low power consumption, dual bridge driver, high drive capability, low voltage drive, low-on resistance, selectable motor operation, built-in Standby and protection features, and more |
Interface | GPIO |
Compatibility | mikroBUS |
Click board size | M (42.9 x 25.4 mm) |
Input Voltage | 3.3V or 5V,External |
PINOUT DIAGRAM
This table shows how the pinout on the DC Motor 19 Click Board™ corresponds to the pinout on the mikroBUS™ socket (the latter shown in the two middle columns).
Notes | Pin | ![]() |
Pin | Notes | |||
---|---|---|---|---|---|---|---|
Motor Control Input 1 | IN1 | 1 | AN | PWM | 16 | IN3 | Motor Control Input 3 |
Motor Control Input 2 | IN2 | 2 | RST | INT | 15 | IN4 | Motor Control Input 4 |
Standby Mode | SBY | 3 | CS | RX | 14 | NC | |
NC | 4 | SCK | TX | 13 | NC | ||
NC | 5 | MISO | SCL | 12 | NC | ||
NC | 6 | MOSI | SDA | 11 | NC | ||
Power Supply | 3.3V | 7 | 3.3V | 5V | 10 | 5V | Power Supply |
Ground | GND | 8 | GND | GND | 9 | GND | Ground |
ONBOARD SETTINGS AND INDICATORS
Label | Name | Default | Description |
---|---|---|---|
LD1 | PWR | - | Power LED Indicator |
JP1 | VCC SEL | Left | Logic Level Voltage Selection 3V3/5V: Left position 3V3, Right position 5V |
JP2 | VM SEL | Left | TC78H653FTG Power Supply Selection VEXT/VCC: Left position VEXT, Right position VCC |
SW1 | LARGE | - | Large-Current Drive Mode Selection Switch |
SW2 | MODE | - | Motor Mode Selection Switch |
DC MOTOR 19 CLICK ELECTRICAL SPECIFICATIONS
Description | Min | Typ | Max | Unit |
---|---|---|---|---|
Supply Voltage VCC | 3.3 | - | 5 | V |
External Power Supply VM | 1.8 | - | 7.5 | V |
Maximum Output Current | - | - | 4 | A |
Operating Temperature Range | -40 | +25 | +105 | °C |
Frequently Asked Questions
Have a Question?
Be the first to ask a question about this.