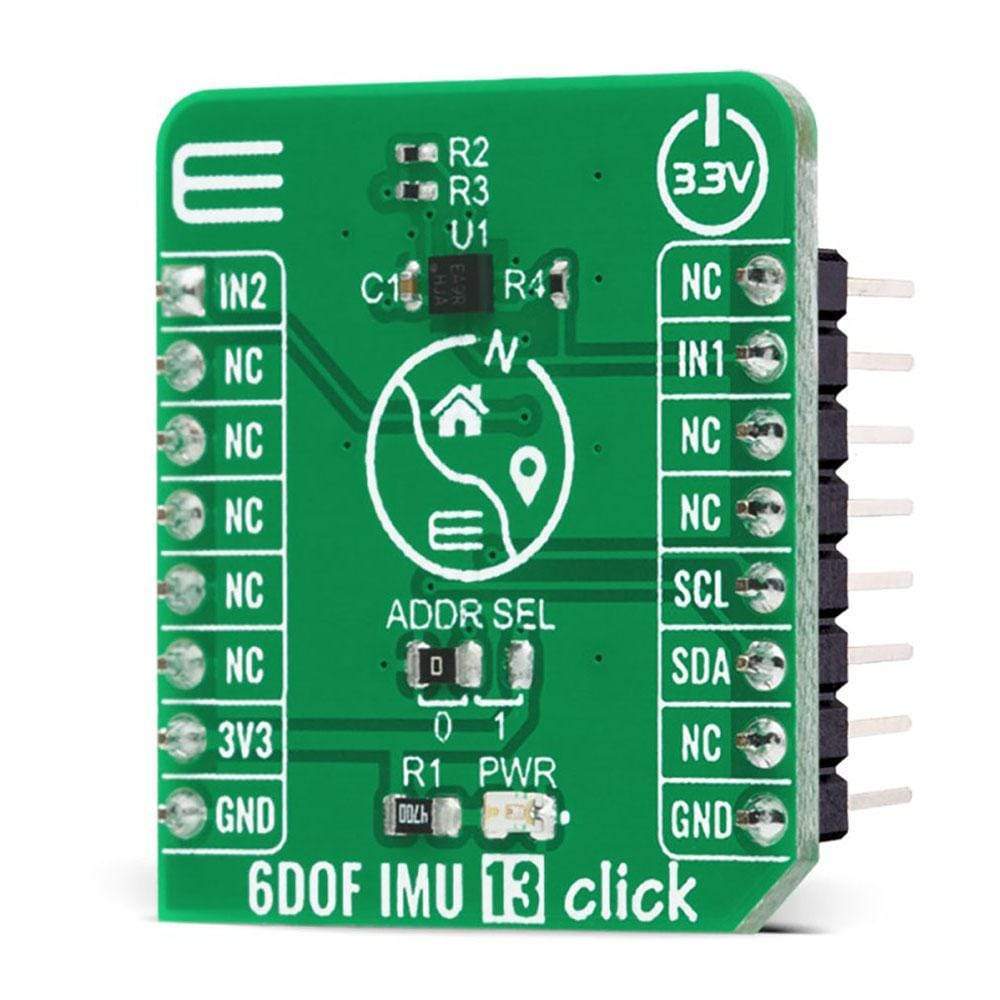
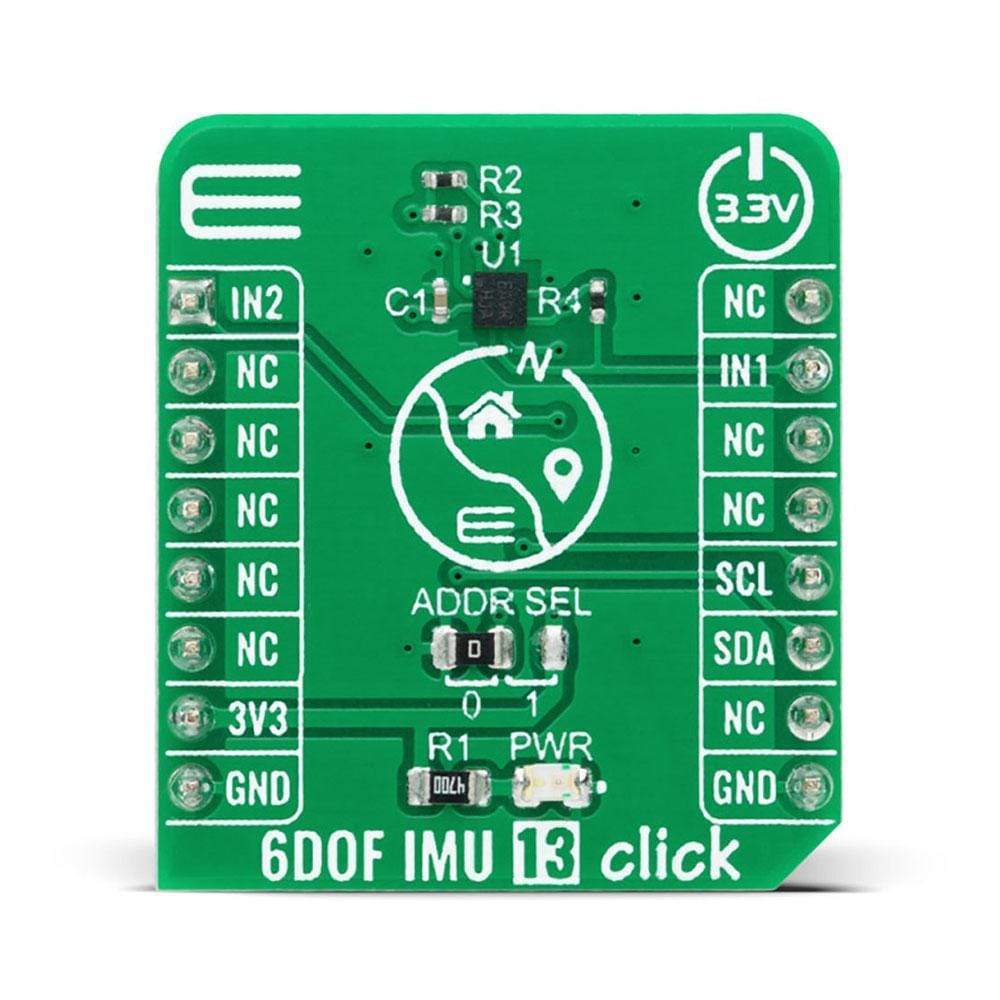
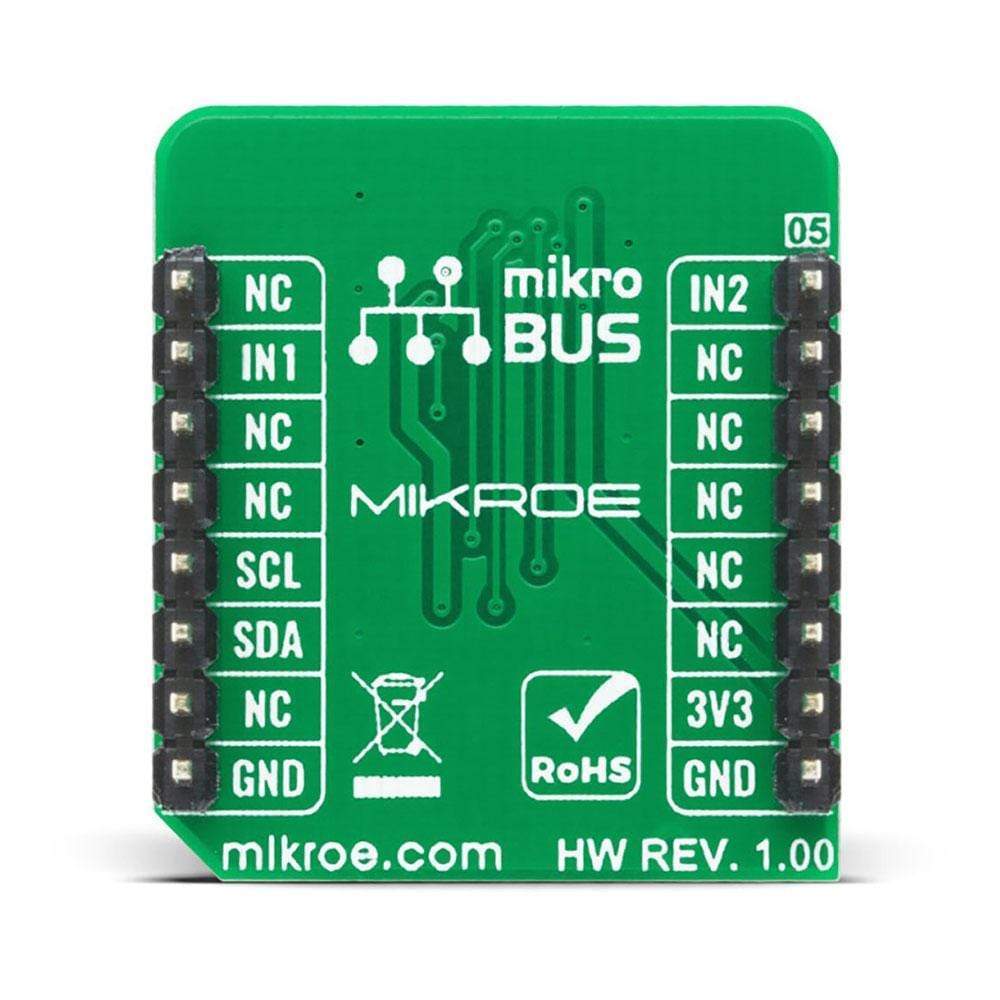
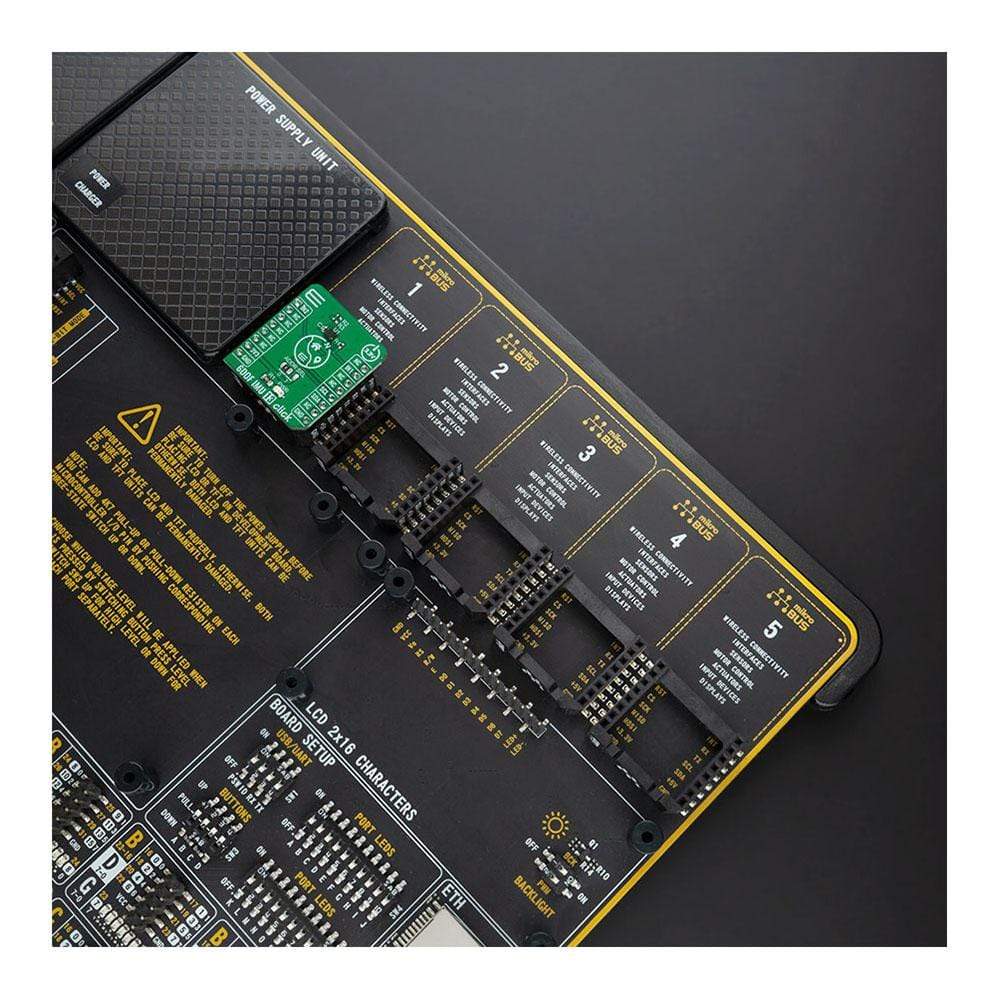
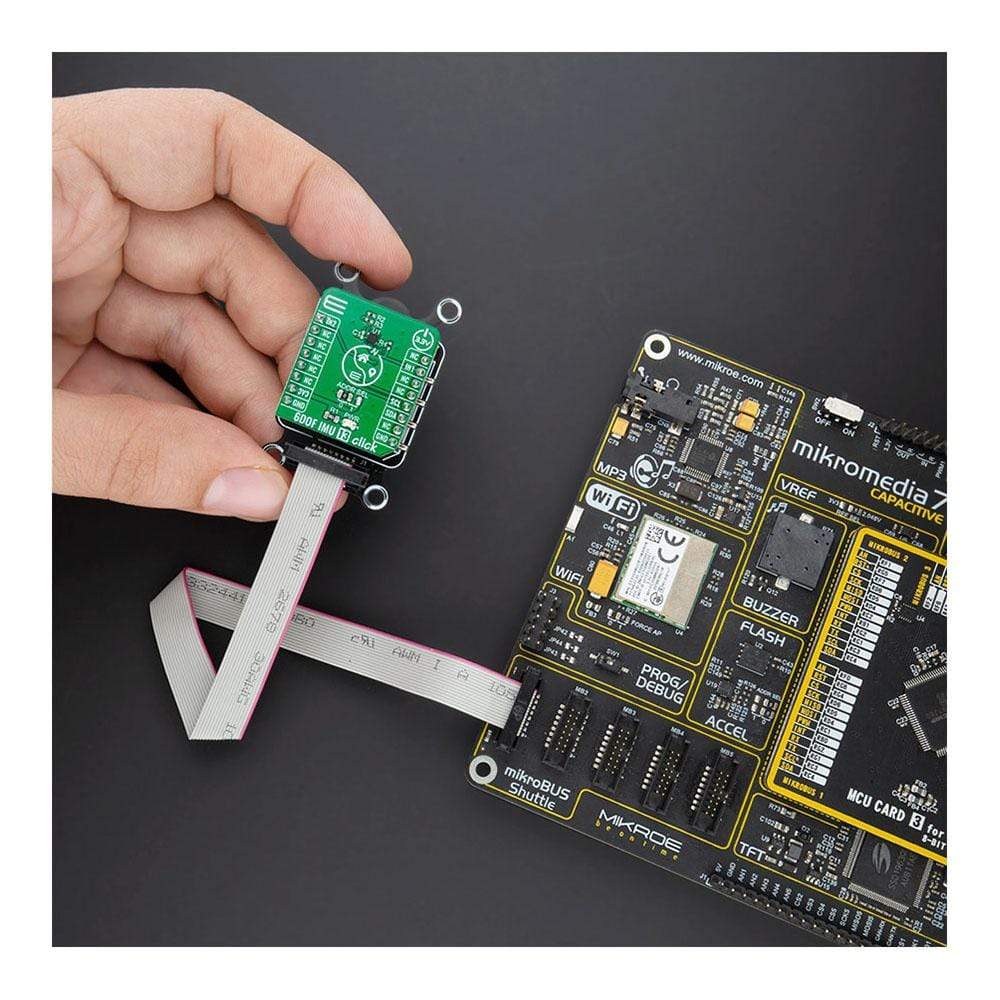

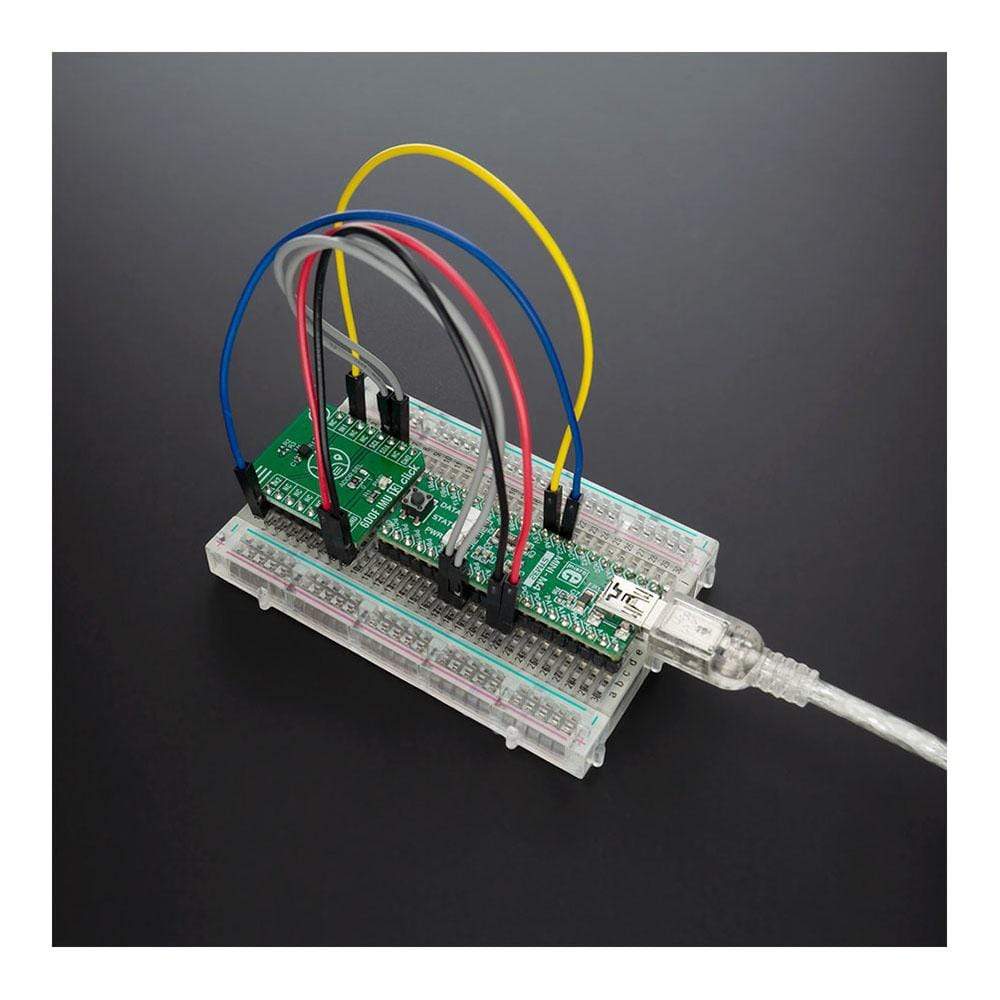
Overview
The 6DOF IMU 13 Click Board™ is a compact add-on board that contains an eCompass that consists of a 3-axis linear accelerometer and a 3-axis magnetic field sensor. This board features the MC6470, an accelerometer and magnetometer for a 6 DoF (6 Degrees of Freedom) sensor solution, from mCube Inc. It has a linear acceleration full-scale range of ±16g and a low noise magnetic sensor with up to 0.15μT magnetic field resolution, with a single I2C interface available to separately control magnetometer and accelerometer functions, enabling independent operation of functions for application flexibility. This Click Board™ is an excellent choice for applications requiring high-precision directional pointing such as map orientation, virtual reality data overlay, enhanced navigation, and gyroscope replacement.
The 6DOF IMU 13 Click is supported by a mikroSDK-compliant library, which includes functions that simplify software development. This Click Board™ comes as a thoroughly tested product, ready to be used on a system equipped with the mikroBUS™ socket.
General Information | |
---|---|
Part Number (SKU) |
MIKROE-4228
|
Manufacturer |
|
Physical and Mechanical | |
Weight |
0.017 kg
|
Other | |
Country of Origin |
|
HS Code Customs Tariff code
|
|
EAN |
8606027380280
|
Warranty |
|
How Does The 6DOF IMU 13 Click Board™ Work?
The 6DOF IMU 13 Click Board™ is based on the MC6470 that combines an accelerometer and magnetometer for a 6 DoF (6 Degrees of Freedom) sensor solution, from mCube Inc. An accelerometer has two states of operation: STANDBY which is his default state after Power-Up function, and WAKE. The STANDBY state offers the lowest power consumption, and only in this state, the I2C interface is active and all register reads and writes are allowed. There is no event detection, sampling, or acceleration measurement in this state. In WAKE state, only write access is permitted to the MODE register. The full-scale acceleration range can be adjusted from ±2g, up to ±16g with a 14-bit resolution.
This 6DOF IMU 13 Click Board™ also includes a high-performance magnetic sensor with 0.15μT resolution, broad field range up to ±2.4mT, and a programmable output data rate from 0.5 to 100 Hz. The magnetometer has two operational modes, Stand-By and Active Mode with Force and Normal State, whose primary purpose is for power management. It also provides additional functions such as Data Ready Function which occurs when new measured results are updated, Offset Calibration and Drift Functions, and Temperature Measurement Function that retrieves temperature data used for internal compensation of output data from an internal temperature sensor. The magnetic sensor output value of each axis is positive when turned toward the magnetic north.
The MC6470 possesses two interrupt outputs, magnetometer (IN2) and an accelerometer (IN1) interrupts, routed to the AN and INT pins on the mikroBUS™ used to signal MCU that an event has been sensed. It also supports directional tap detection in ±X, ±Y, or ±Z axis, where each axis is independent, although only one direction per axis is supported simultaneously. In this case, the interrupt pins can be used to indicate that a tap event has been detected.
The 6DOF IMU 13 Click Board™ communicates with MCU using the standard I2C 2-Wire interface with a maximum frequency of 400kHz. The MC6470 always operates as an I2C slave device on both magnetometer and accelerometer I2C interfaces and allows the choice of the least significant bit (LSB) of its I2C slave address which can be done by using the SMD jumper labelled as ADDR SEL.
This Click Board™ is designed to be operated only with a 3.3V logic level. A proper logic voltage level conversion should be performed before the Click board™ is used with MCUs with different logic levels.
Specifications
Type | Acceleration,Magnetic,Motion |
Applications | Can be used for applications where there is a need for high-precision directional pointing such as map orientation, virtual reality data overlay, enhanced navigation, and gyroscope replacement. |
On-board modules | 6DOF IMU 13 Click is based on the MC6470, 6 DoF solution, a 3-axis accelerometer, and 3-axis magnetometer sensors, from mCube Inc. |
Key Features | Low power consumption, high precision, programmable interrupts, user scalable accel full-scale range, programmable output data rate, and more. |
Interface | I2C |
Compatibility | mikroBUS |
Click board size | S (28.6 x 25.4 mm) |
Input Voltage | 3.3V |
Pinout diagram
This table shows how the pinout on 6DOF IMU 13 Click Board™ corresponds to the pinout on the mikroBUS™ socket (the latter shown in the two middle columns).
Notes | Pin | ![]() |
Pin | Notes | |||
---|---|---|---|---|---|---|---|
Magnet. Interrupt | IN2 | 1 | AN | PWM | 16 | NC | |
NC | 2 | RST | INT | 15 | IN1 | Accel. Interrupt | |
NC | 3 | CS | RX | 14 | NC | ||
NC | 4 | SCK | TX | 13 | NC | ||
NC | 5 | MISO | SCL | 12 | SCL | I2C Clock | |
NC | 6 | MOSI | SDA | 11 | SDA | I2C Data | |
Power Supply | 3.3V | 7 | 3.3V | 5V | 10 | NC | |
Ground | GND | 8 | GND | GND | 9 | GND | Ground |
Onboard settings and indicators
Label | Name | Default | Description |
---|---|---|---|
LD1 | PWR | - | Power LED Indicator |
JP1 | ADDR SEL | Left | I2C Address Selection: Left position 0, Right position 1 |
6DOF IMU 13 Click electrical specifications
Description | Min | Typ | Max | Unit |
---|---|---|---|---|
Supply Voltage | -0.3 | 3.3 | 3.6 | V |
Acceleration (any axis) | - | - | 10.000 | g |
Acceleration Sensitivity | 8 | - | 4096 | LSB/g |
Magnetometer Field Range | -2.4 | - | 2.4 | mT |
Magnetometer Sensitivity | - | 0.15 | - | µT / LSB |
Operating Temperature Range | -40 | - | +85 | °C |
Frequently Asked Questions
Have a Question?
Be the first to ask a question about this.