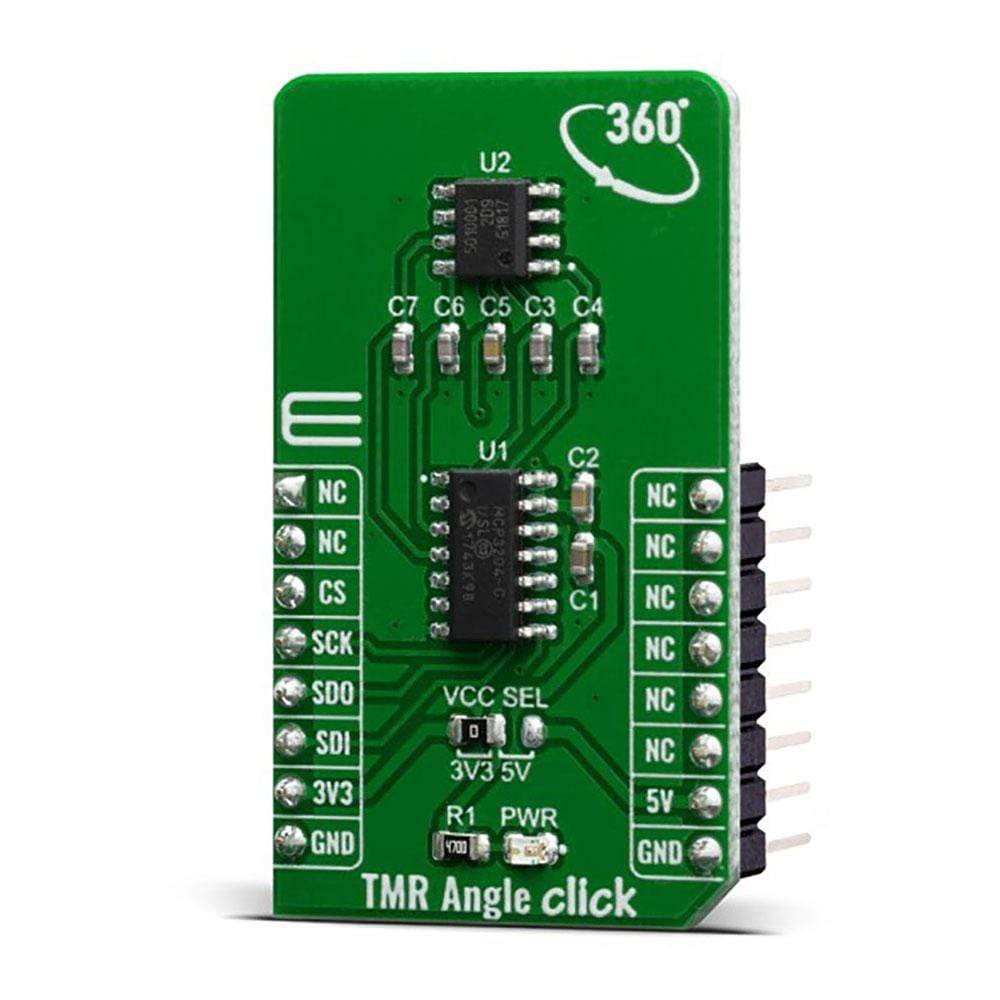
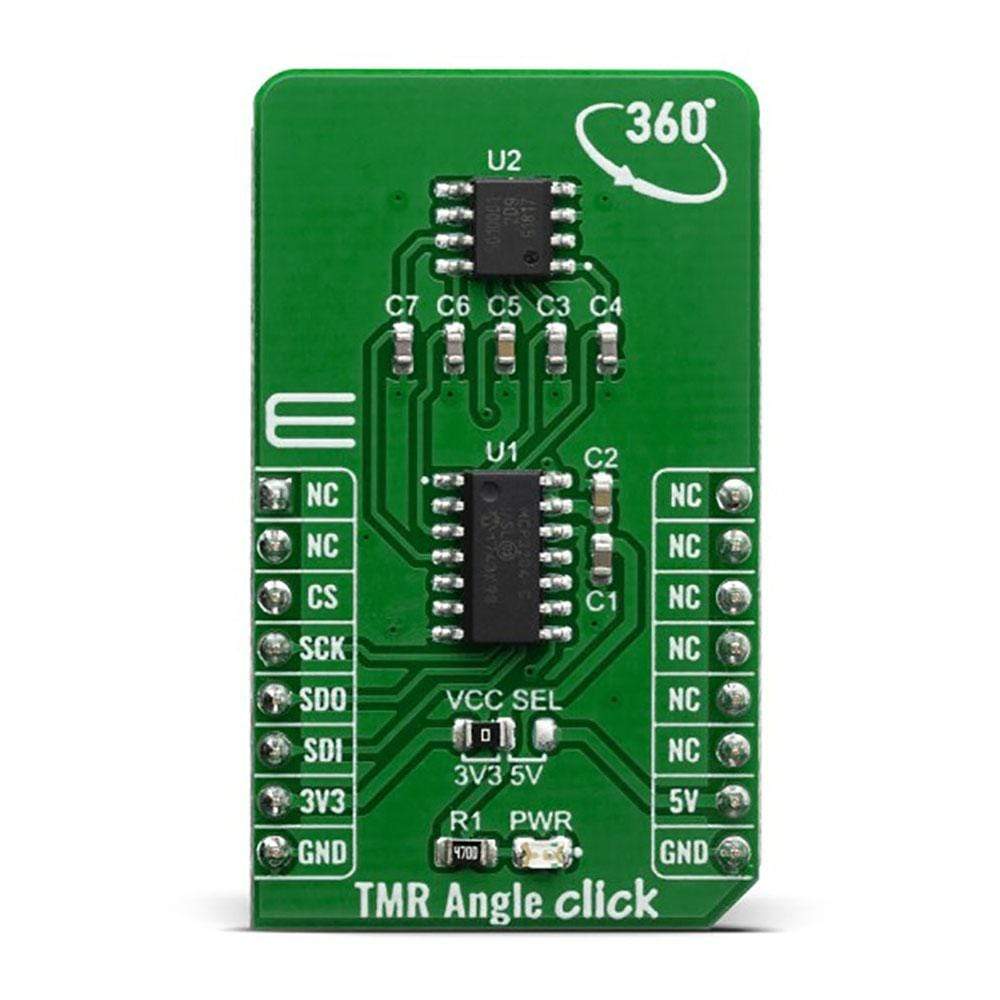
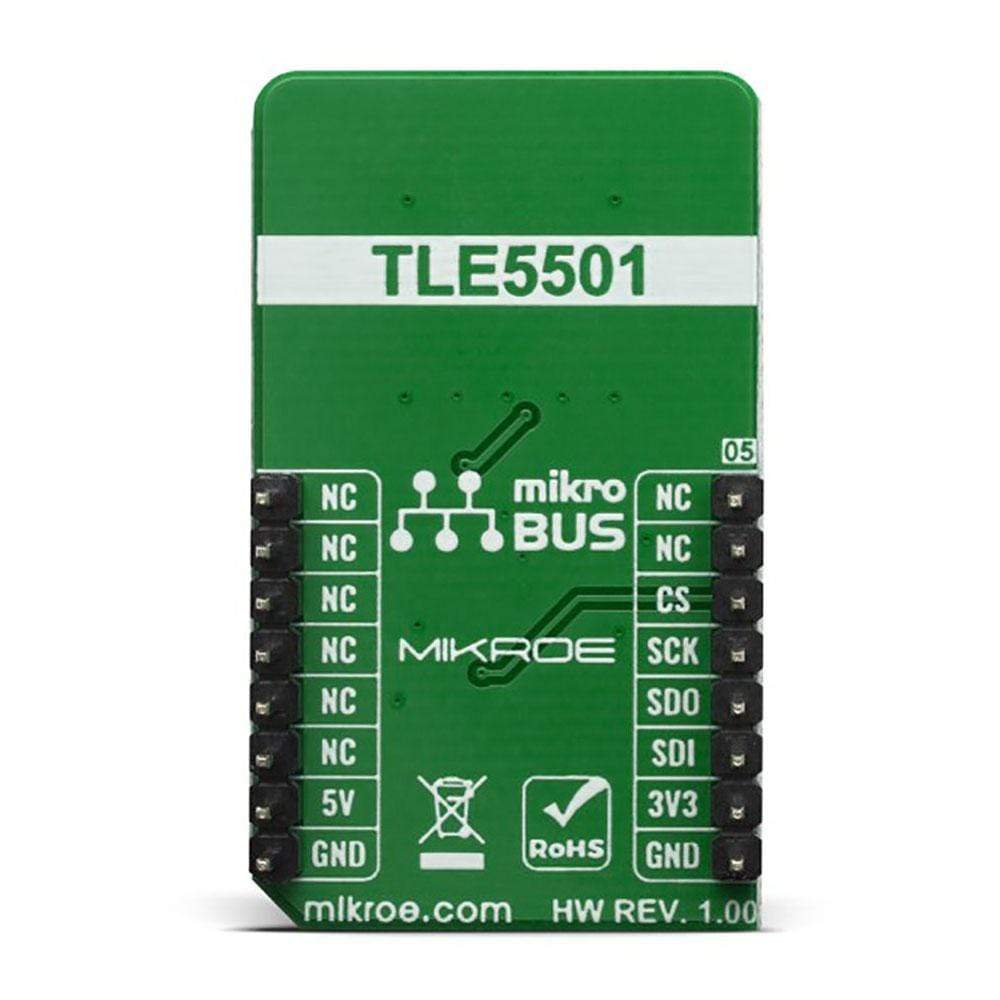
Overview
The TMR Angle Click Board™ is perfectly suited for developing applications that range from steering angle applications with the highest functional safety requirements to motors for wipers, pumps and actuators and electric motors in general. This is thanks to the TLE5501, which is dedicated to any automotive but also industrial and consumer applications like robotics or gimbal.
The TMR Angle Click Board™ is supported by a mikroSDK compliant library, which includes functions that simplify software development. This Click board™ comes as a fully tested product, ready to be used on a system equipped with the mikroBUS™ socket.
General Information | |
---|---|
Part Number (SKU) |
MIKROE-3769
|
Manufacturer |
|
Physical and Mechanical | |
Weight |
0.021 kg
|
Other | |
Country of Origin |
|
HS Code Customs Tariff code
|
|
EAN |
8606018717026
|
Warranty |
|
How Does The TMR Angle Click Board™ Work?
The TMR Angle Click Board™ contains the TLE5501 from Infineon Technologies AG – analog TMR-based angle sensors for any kind of angular position sensing from Infineon, and the MCP3204, a converter with SPI serial interface from Microchip. Regarding the TLE5501, the application fields range from steering angle applications with the highest functional safety requirements to motors for wipers, pumps and actuators and electric motors in general. TLE5501 is dedicated to any automotive but also industrial and consumer applications like robotics or gimbal.
Some of its key features include large output signals of up to 0.37 V/V for easy analog value readout, discrete bridge with differential sine and cosine output, a very low supply current < 2.5 mA, a magnetic field range 20 mT to 100 mT and a Typ. angle error < 1.0° (over the whole temperature and lifetime profile). It has been primarily designed for safety.
One major benefit of the Infineon TMR technology is its high sensing sensitivity coming with a high output voltage. So unlike other technologies, a TMR based sensor does not require any additional internal amplifier. Thus the sensor can be connected directly to the microcontroller without any further amplification – saving costs for the end customer. There is yet another cost saving aspect of Infineon's TMR technology. TMR shows a very low temperature drift reducing external calibration and compensation efforts. In addition, the TMR technology is also well known for its low current consumption.
When it comes to reading the output analog value, the MCP3204 is used – a 4-Channel A/D converter with SPI serial interface, from Microchip, it is ideally suited for sensor interface, process control, data acquisition and battery operated systems. It has a 12-bit resolution, and it is programmable to provide two pseudo-differential input pairs or four single-ended inputs. Configuration is done as part of the serial command before each conversion begins. When used in the pseudodifferential mode, each channel pair (i.e., CH0 and CH1, CH2 and CH3 etc.) On this Click board™ the output sin and cos signals are wired as a pseudo-differential input signals to the MCP3204.
Communication with the devices is accomplished using a simple serial interface compatible with the SPI protocol. The devices are capable of conversion rates of up to 100 ksps. The MCP3204/3208 devices operate over a broad voltage range (2.7V - 5.5V).
The TMR Angle Click Board™ offers a selection between 3.3V and 5V operation, with the onboard SMD jumper, labelled as PWR SEL. This allows both 3.3V and 5V MCUs to be interfaced with this Click board™.
SPECIFICATIONS
Type | Magnetic |
Applications | The application fields range from steering angle applications with the highest functional safety requirements to motors for wipers, pumps and actuators and electric motors in general. |
On-board modules | TLE5501, magnetic sensor from Infineon and MCP3204, a converter with SPI serial interface from Microchip |
Key Features | large output signals for easy analog value readout, discrete bridge with differential sine and cosine output, a very low supply current 2.5 mA, a magnetic field range 20 mT to 100 mT |
Interface | SPI |
Compatibility | mikroBUS |
Click board size | M (42.9 x 25.4 mm) |
Input Voltage | 3.3V or 5V |
PINOUT DIAGRAM
This table shows how the pinout of the TMR Angle Click Board™ corresponds to the pinout on the mikroBUS™ socket (the latter shown in the two middle columns).
Notes | Pin | ![]() |
Pin | Notes | |||
---|---|---|---|---|---|---|---|
NC | 1 | AN | PWM | 16 | NC | ||
NC | 2 | RST | INT | 15 | NC | ||
Chip Select | CS | 3 | CS | RX | 14 | NC | |
SPI Clock | SCK | 4 | SCK | TX | 13 | NC | |
SPI Data Out | SDO | 5 | MISO | SCL | 12 | NC | |
SPI Data Out | SDI | 6 | MOSI | SDA | 11 | NC | |
Power Supply | 3.3V | 7 | 3.3V | 5V | 10 | 5V | Power Supply |
Ground | GND | 8 | GND | GND | 9 | GND | Ground |
ONBOARD SETTINGS AND INDICATORS
Label | Name | Default | Description |
---|---|---|---|
LD1 | PWR | - | Power LED Indicator |
Frequently Asked Questions
Have a Question?
Be the first to ask a question about this.