
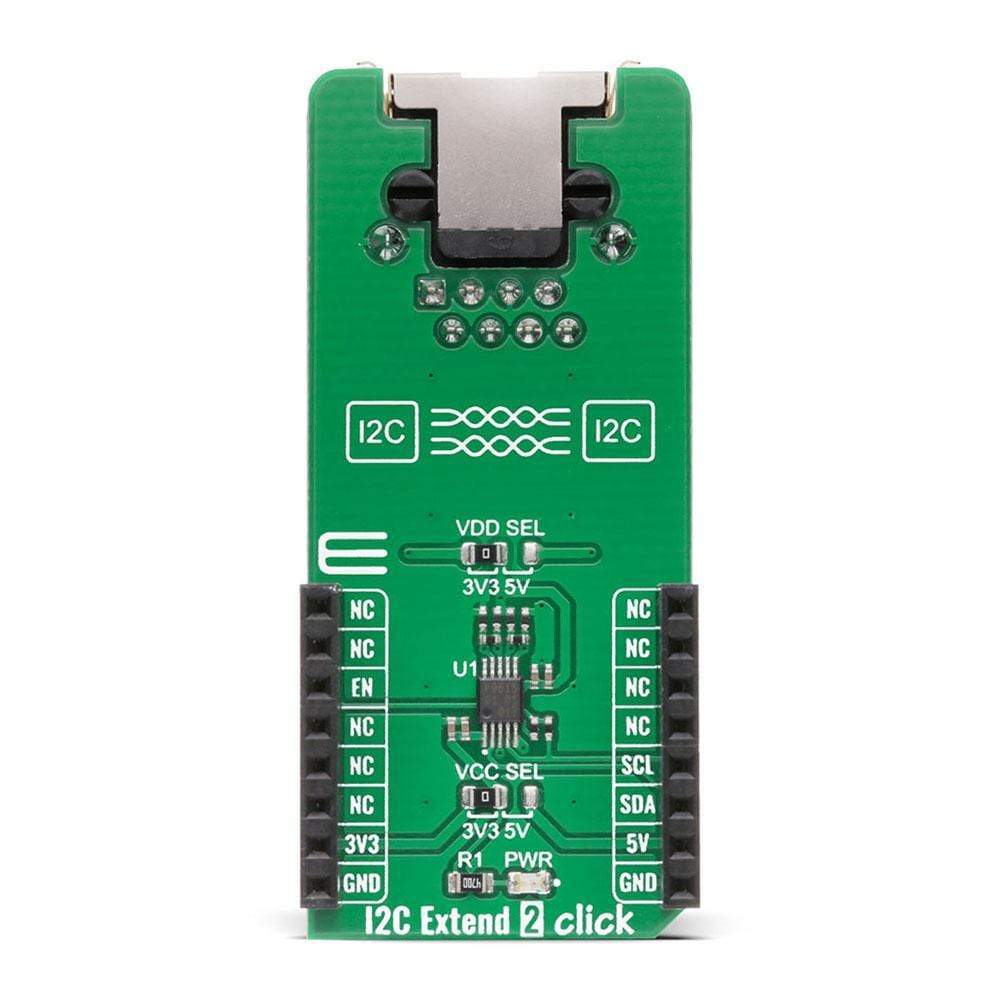
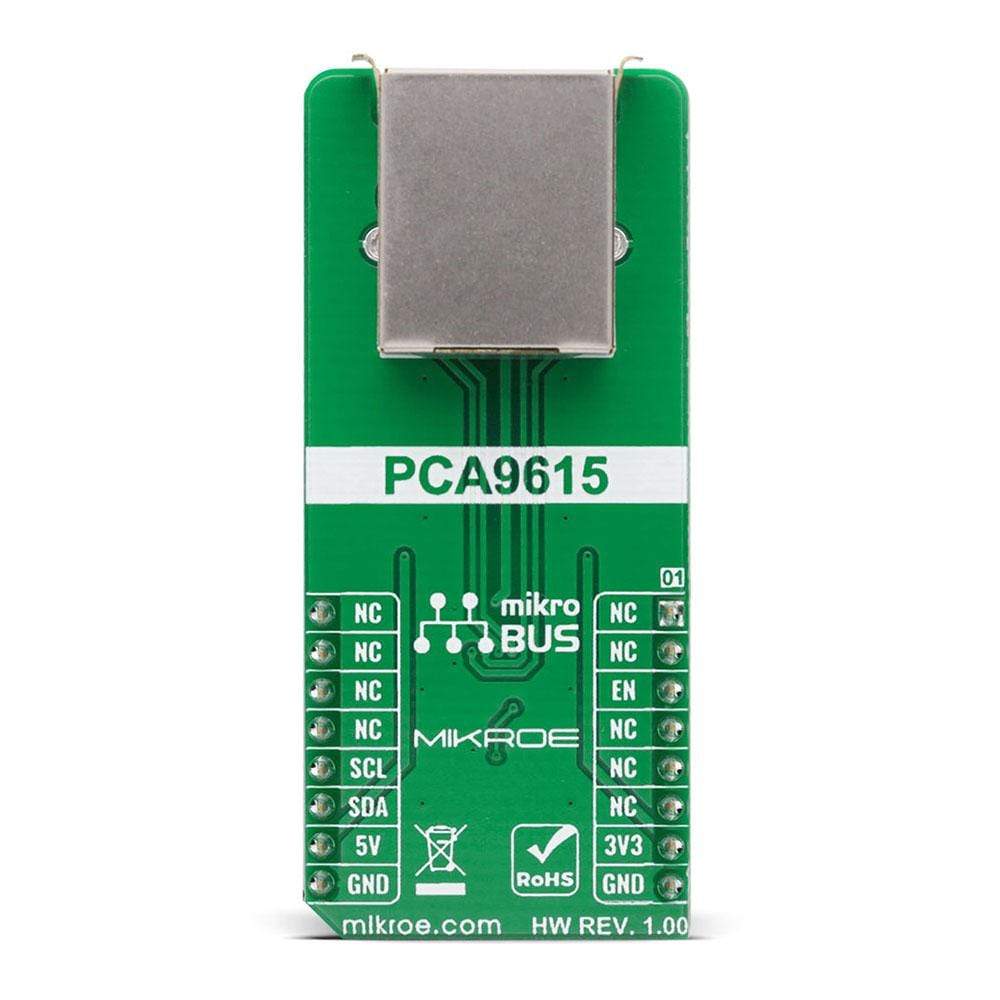
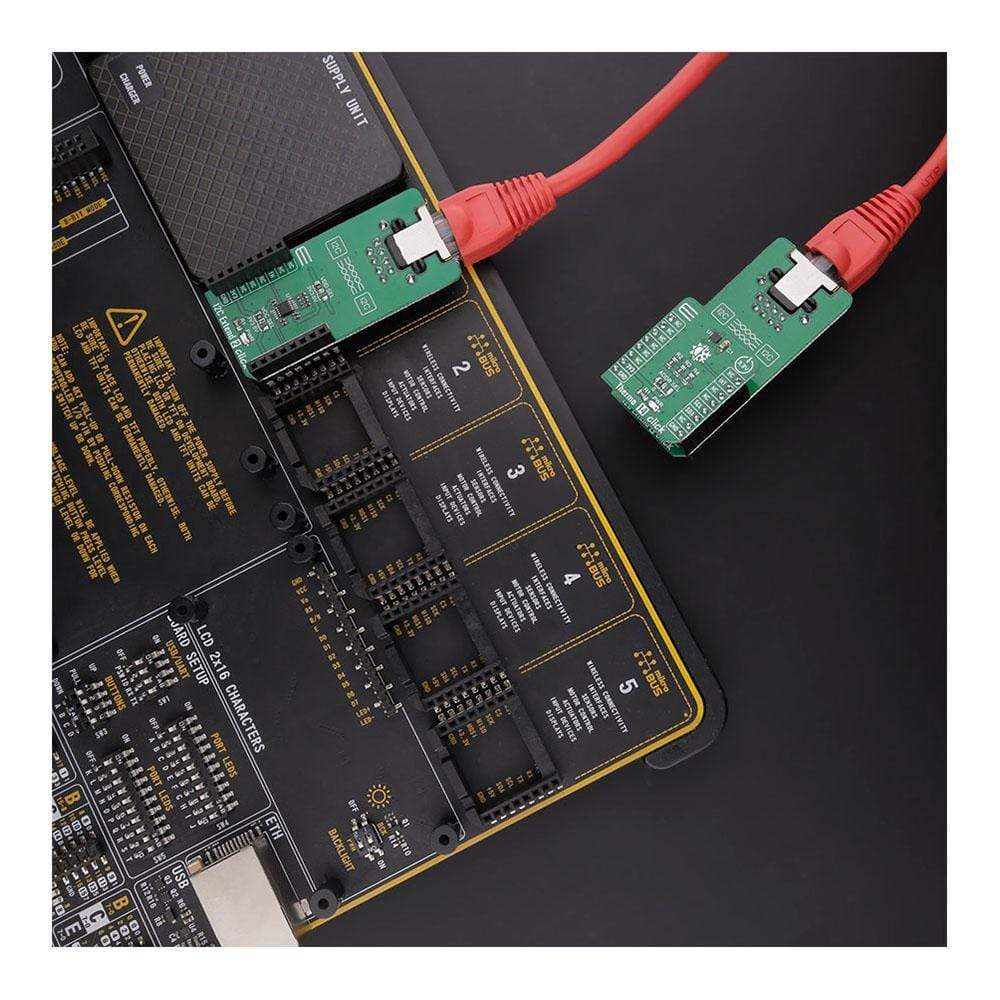
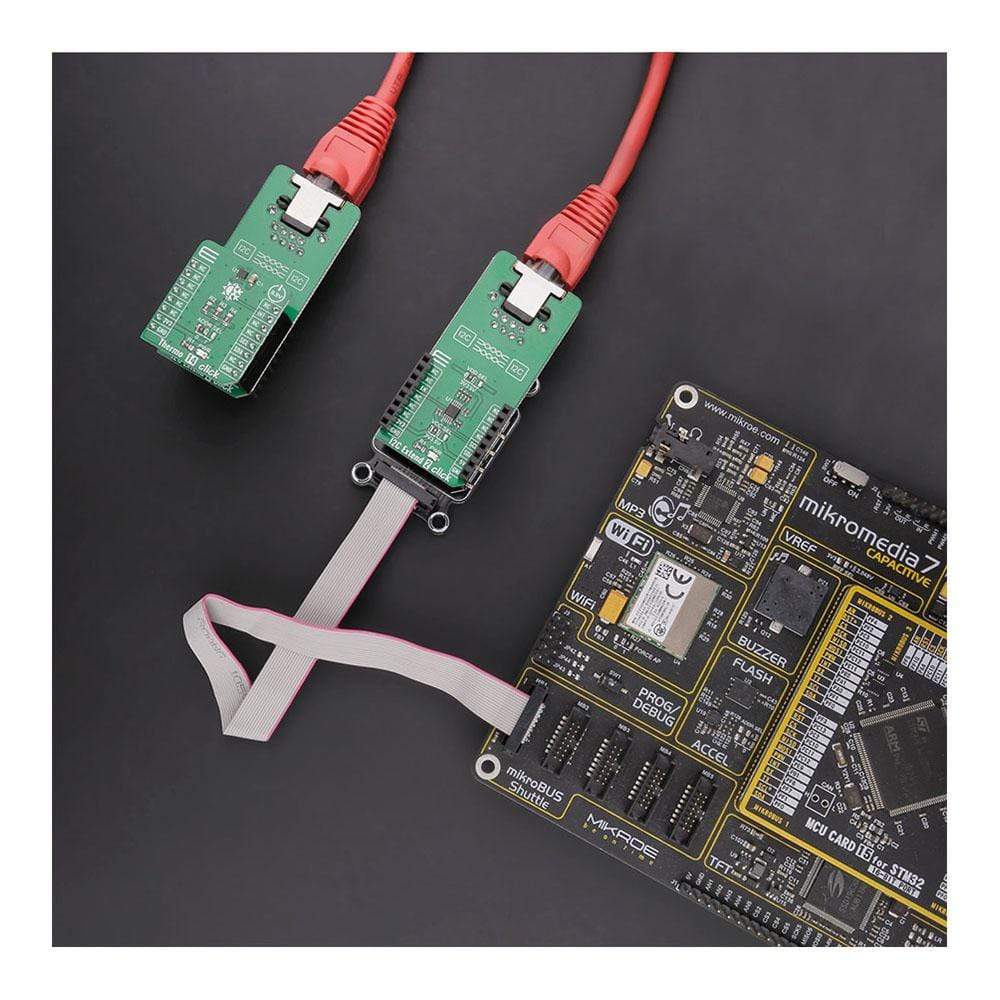
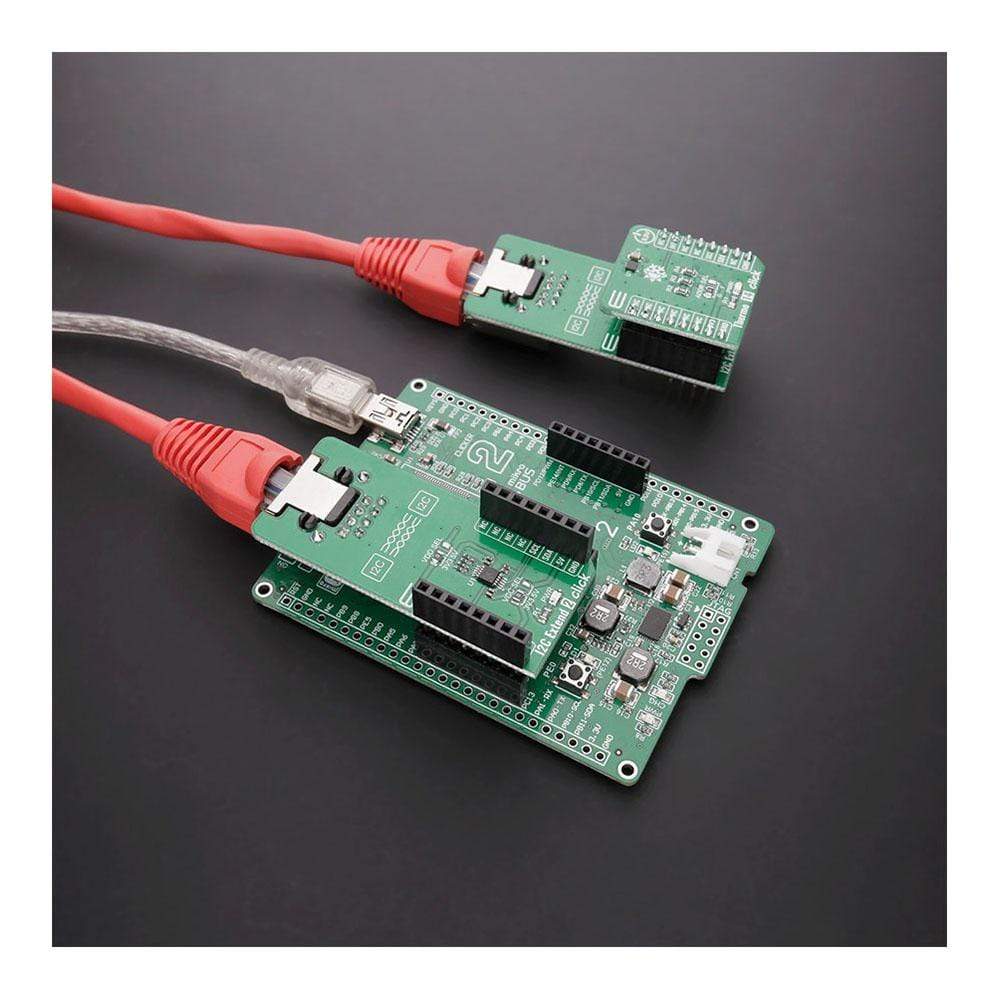
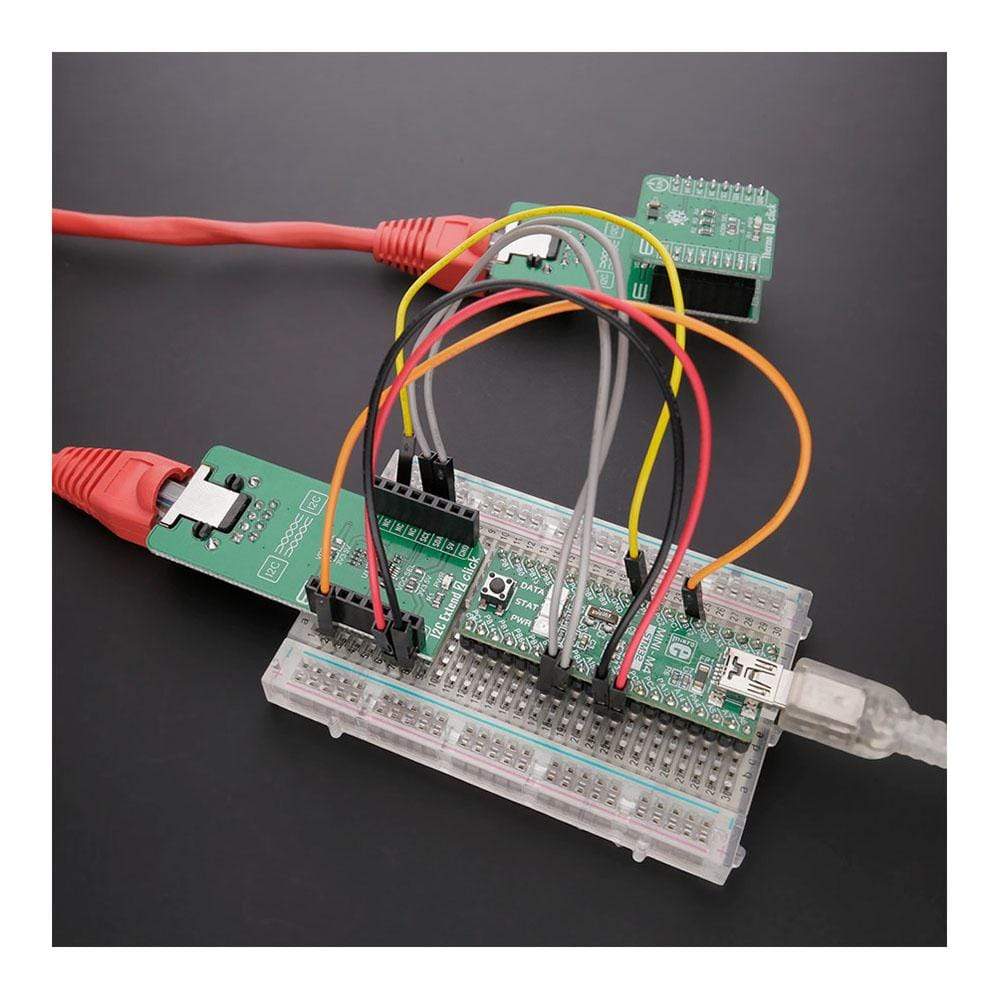
Overview
The I2C Extend 2 Click Board™ is a compact add-on board suitable for I2C communication bus extension. This board features the PCA9615, a 2-channel multipoint differential I2C bus buffer with hot-swap logic from NXP Semiconductors. The PCA9615 converts the two default I2C signals into four differential signals, two for SCL and two for SDA. The differential signals allow the I2C signals to reach distances of up to 3m while maintaining their signal integrity sent over an Ethernet cable through the onboard RJ-45 connector. This Click Board™ is suitable for various applications that require extending the I2C bus over a long distance, such as commercial lighting and industrial control, control of power supplies in a high noise environment, and more.
The I2C Extend 2 Click Board™ is supported by a mikroSDK compliant library, which includes functions that simplify software development. This Click Board™ comes as a fully tested product, ready to be used on a system equipped with the mikroBUS™ socket.
General Information | |
---|---|
Part Number (SKU) |
MIKROE-4419
|
Manufacturer |
|
Physical and Mechanical | |
Weight |
0.023 kg
|
Other | |
Country of Origin |
|
HS Code Customs Tariff code
|
|
EAN |
8606027381218
|
Warranty |
|
How Does The I2C Extend 2 Click Board™ Work?
The I2C Extend 2 Click Board™ is based on the PCA9615, a Fast-Mode Plus (FM+) I2C bus buffer that extends the single-ended I2C bus through electrically noisy environments from NXP Semiconductor. It consists of two single-ended to differential driver channels for the SCL (Serial Clock) and SDA (Serial Data). The use of differential transmission lines between identical I2C bus buffers removes electrical noise and common-mode offsets that are present when signal lines must pass between different voltage domains, such as high energy power supplies and electric motors. Those signals can reach distances of up to 3m or longer at lower clock speeds while maintaining signal integrity sent over an Ethernet cable (a twisted-pair transmission line cable) through the onboard RJ-45 connector.
The PCA9615 converts the two default I2C signals into four differential signals, two for SCL and two for SDA. The signal direction is determined by the I2C protocol, which means it does not require a direction signal, as these bus buffers automatically set signal flow direction. Additional circuitry allows the PCA9615 to be used for 'hot-swap' applications, where systems are always ON but require insertion or removal of modules or cards without disruption to existing signals. Because the supply voltages on the I2C bus side may be different from the external I2C bus side, there are two power supply pins and common ground. First is a standard I2C bus side power supply selected via the VCC SEL jumper, and the other represents the majority supply for circuitry determined by the VDD SEL jumper.
The I2C Extend 2 Click Board™ communicates with MCU using the standard I2C interface with a frequency up to 100kHz in the Standard and 400kHz in the Fast Mode, and up to 1MHz in the Fast Mode Plus. The user must be cautious not to overload the driver's current rating of 3mA for Standard and Fast Modes and 30mA for Fast Mode Plus (FM+). Also, this Click board™ has an Enable pin, routed on the CS pin of the mikroBUS™ socket labelled as EN, used to disable the bus buffer, and is useful for fault finding, Power-Up sequencing, or re-configuration of a bus system by isolating sections not needed at all times.
The I2C Extend 2 Click Board™ is designed to operate with both 3.3V and 5V logic voltage levels selected via the VCC SEL jumper. It allows for both 3.3V and 5V capable MCUs to use the I2C communication lines properly. However, the Click board™ comes equipped with a library that contains easy to use functions and an example code which can be used, as a reference, for further development.
SPECIFICATIONS
Type | I2C |
Applications | Can be used for various applications that require extending the I2C bus over a long distance, such as commercial lighting and industrial control, control of power supplies in a high noise environment, and more. |
On-board modules | IThe I2C Extend 2 Click Board™ is based on the PCA9615, a Fast-Mode Plus (FM+) I2C bus buffer that extends the single-ended I2C bus through electrically noisy environments from NXP Semiconductor. |
Key Features | Low power consumption, improved resistance to system noise, hot swap, supports arbitration and clock stretching, bus idle detect, and more. |
Interface | I2C |
Compatibility | mikroBUS |
Click board size | L (57.15 x 25.4 mm) |
Input Voltage | 3.3V or 5V |
PINOUT DIAGRAM
This table shows how the pinout of the I2C Extend 2 Click Board™ corresponds to the pinout on the mikroBUS™ socket (the latter shown in the two middle columns).
Notes | Pin | ![]() |
Pin | Notes | |||
---|---|---|---|---|---|---|---|
NC | 1 | AN | PWM | 16 | NC | ||
NC | 2 | RST | INT | 15 | NC | ||
Enable | EN | 3 | CS | RX | 14 | NC | |
NC | 4 | SCK | TX | 13 | NC | ||
NC | 5 | MISO | SCL | 12 | SCL | I2C Clock | |
NC | 6 | MOSI | SDA | 11 | SDA | I2C Data | |
Power Supply | 3.3V | 7 | 3.3V | 5V | 10 | 5V | Power Supply |
Ground | GND | 8 | GND | GND | 9 | GND | Ground |
ONBOARD SETTINGS AND INDICATORS
Label | Name | Default | Description |
---|---|---|---|
LD1 | PWR | - | Power LED Indicator |
JP1 | VCC SEL | Left | Power Supply Voltage Selection 3V3/5V: Left position 3V3, Right position 5V |
JP2 | VDD SEL | Left | Differential Side Voltage Selection 3V3/5V: Left position 3V3, Right position 5V |
I2C EXTEND 2 CLICK ELECTRICAL SPECIFICATIONS
Description | Min | Typ | Max | Unit |
---|---|---|---|---|
Supply Voltage | -0.5 | - | 6 | V |
Maximum Output Current | - | - | 80 | mA |
Data Rate | - | - | 1 | MHz |
Operating Temperature Range | -40 | - | +85 | °C |
Frequently Asked Questions
Have a Question?
Be the first to ask a question about this.