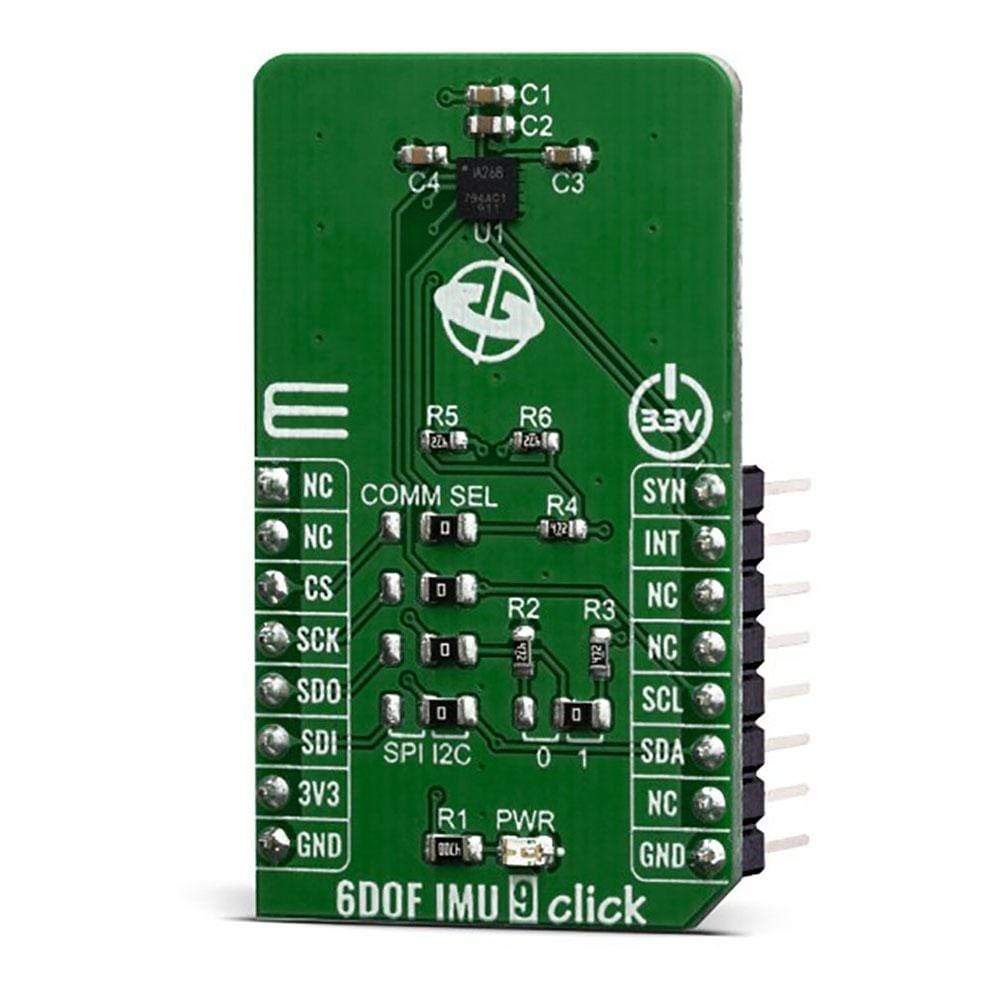
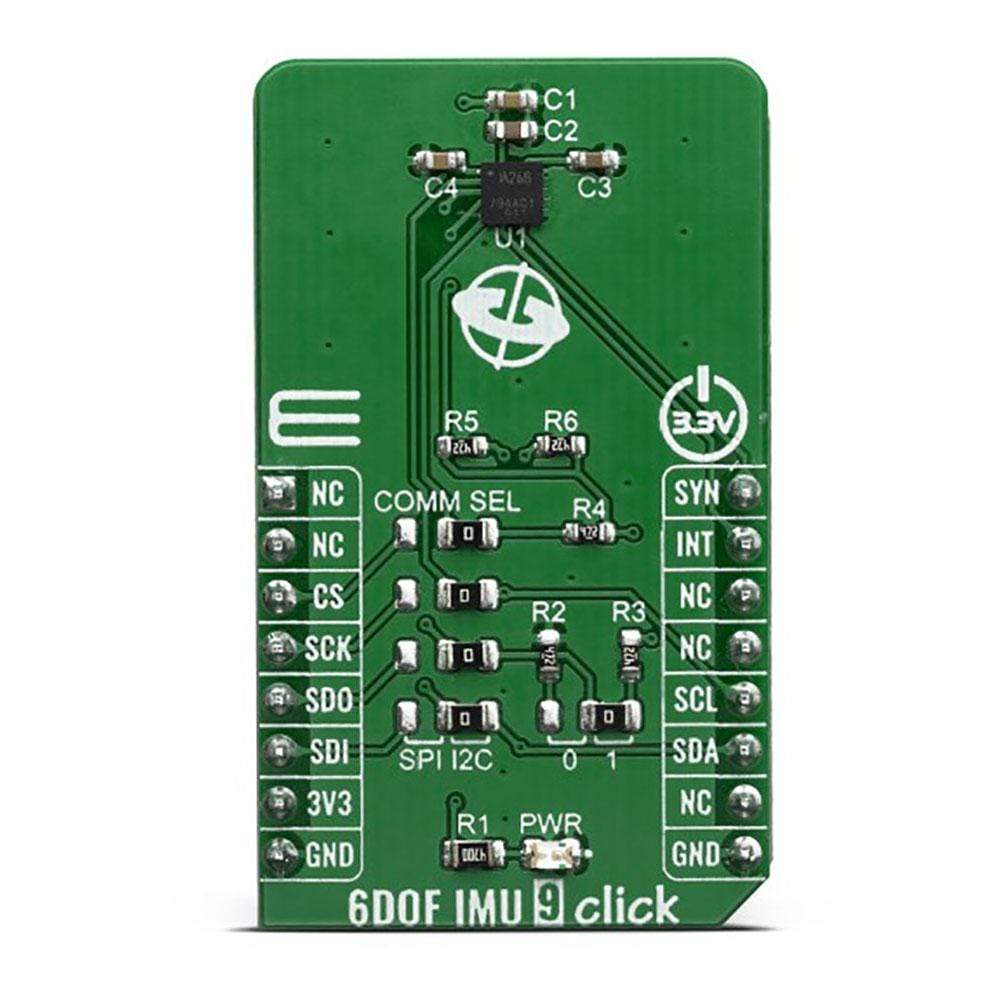

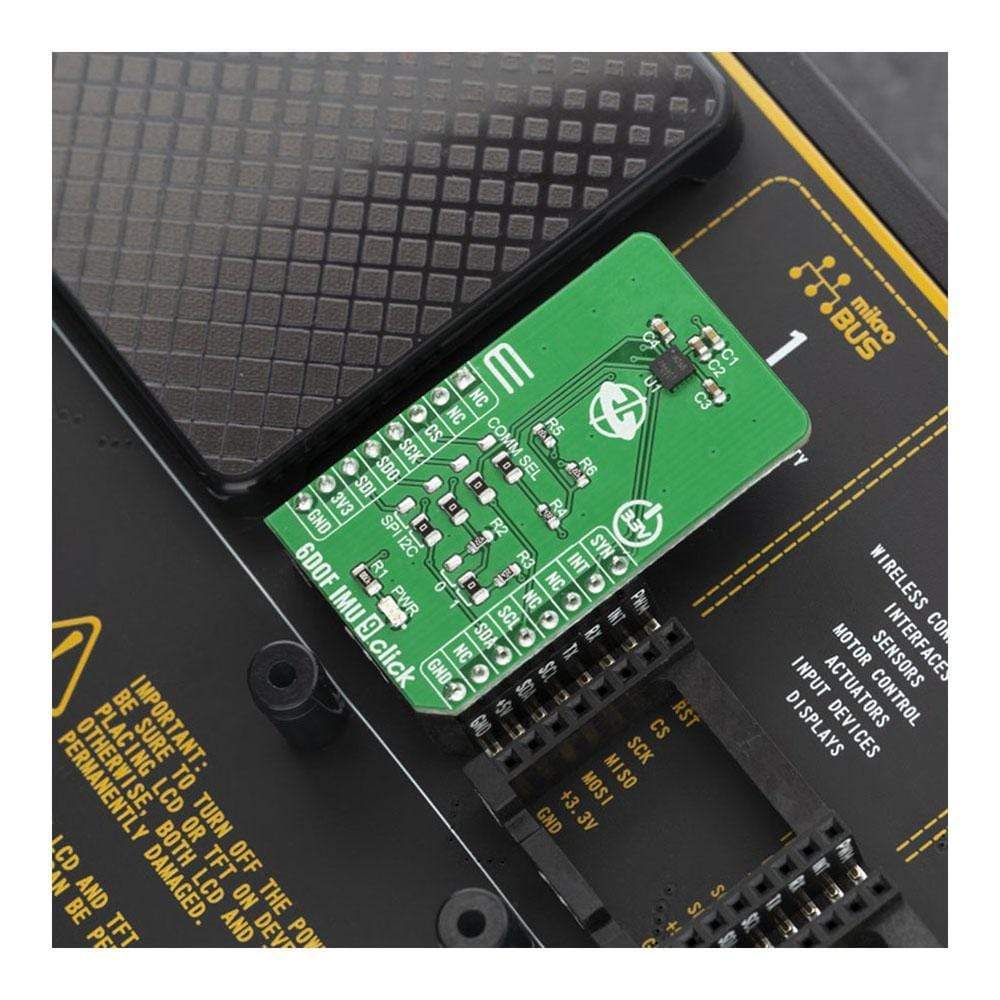
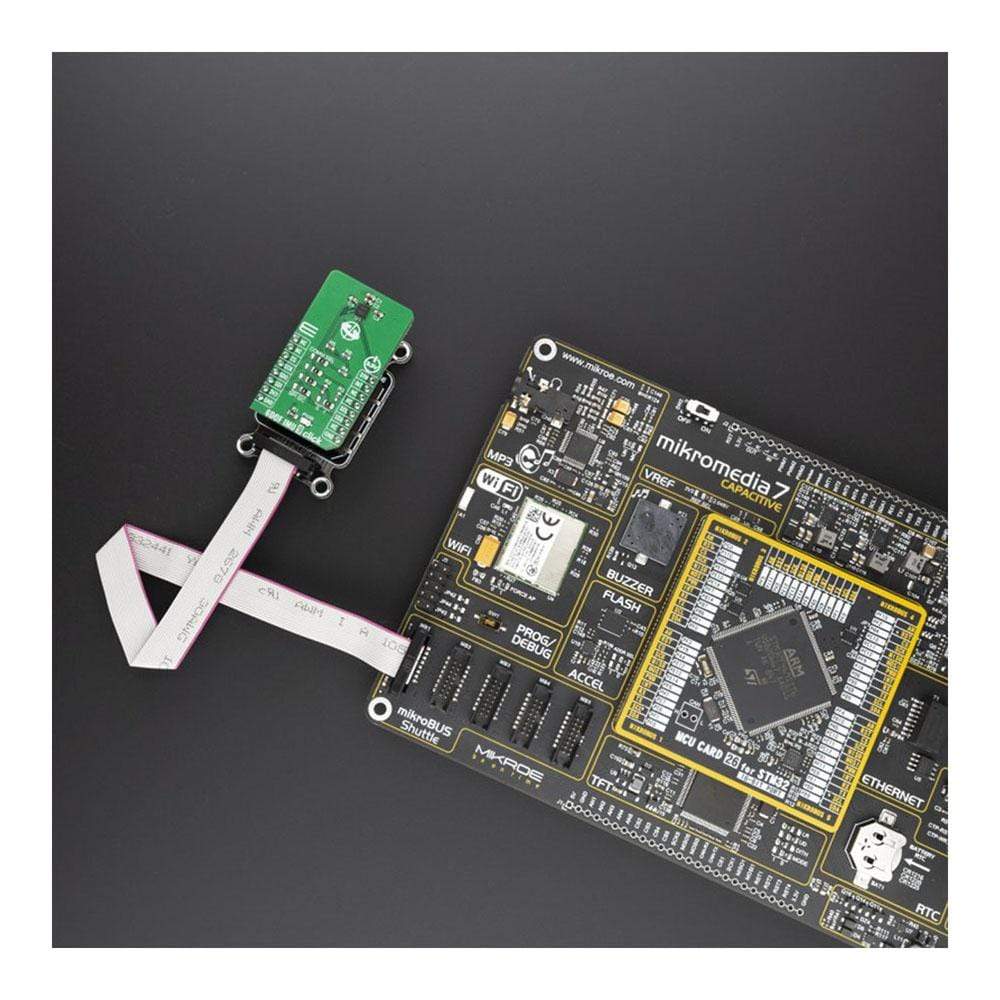
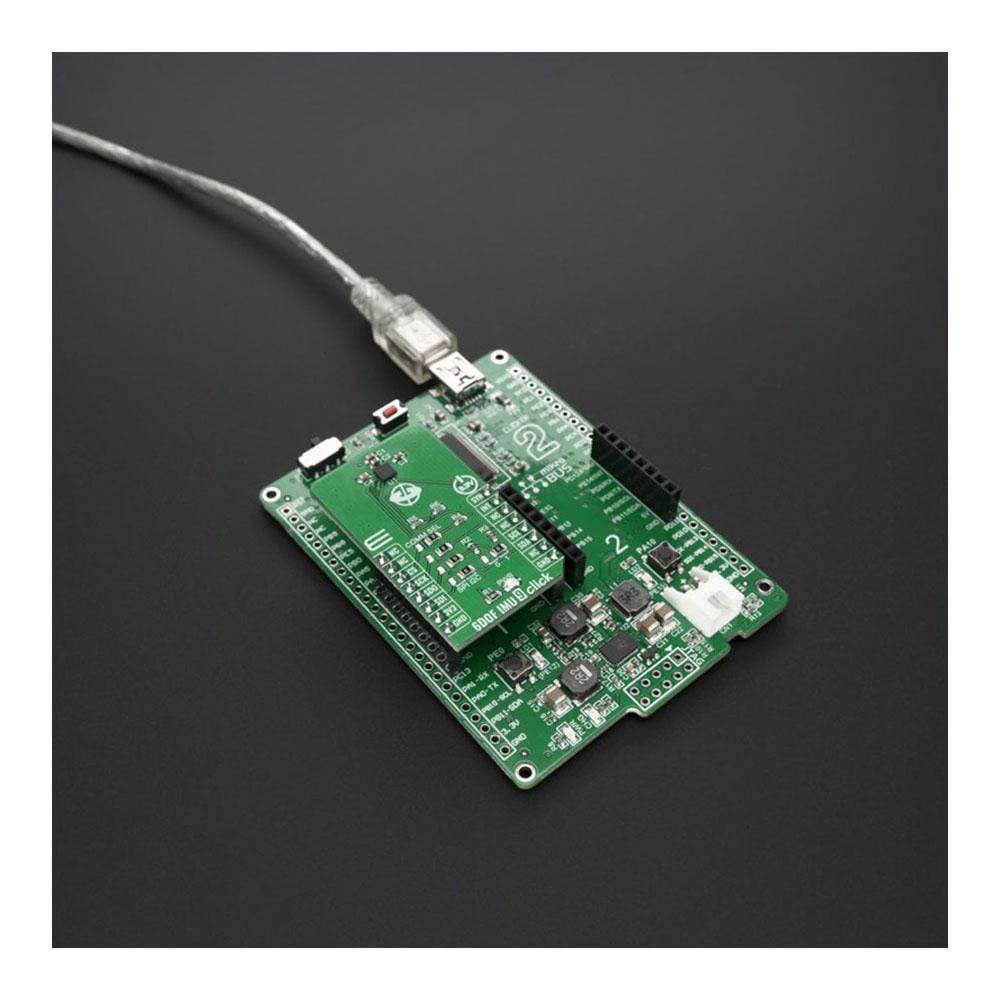
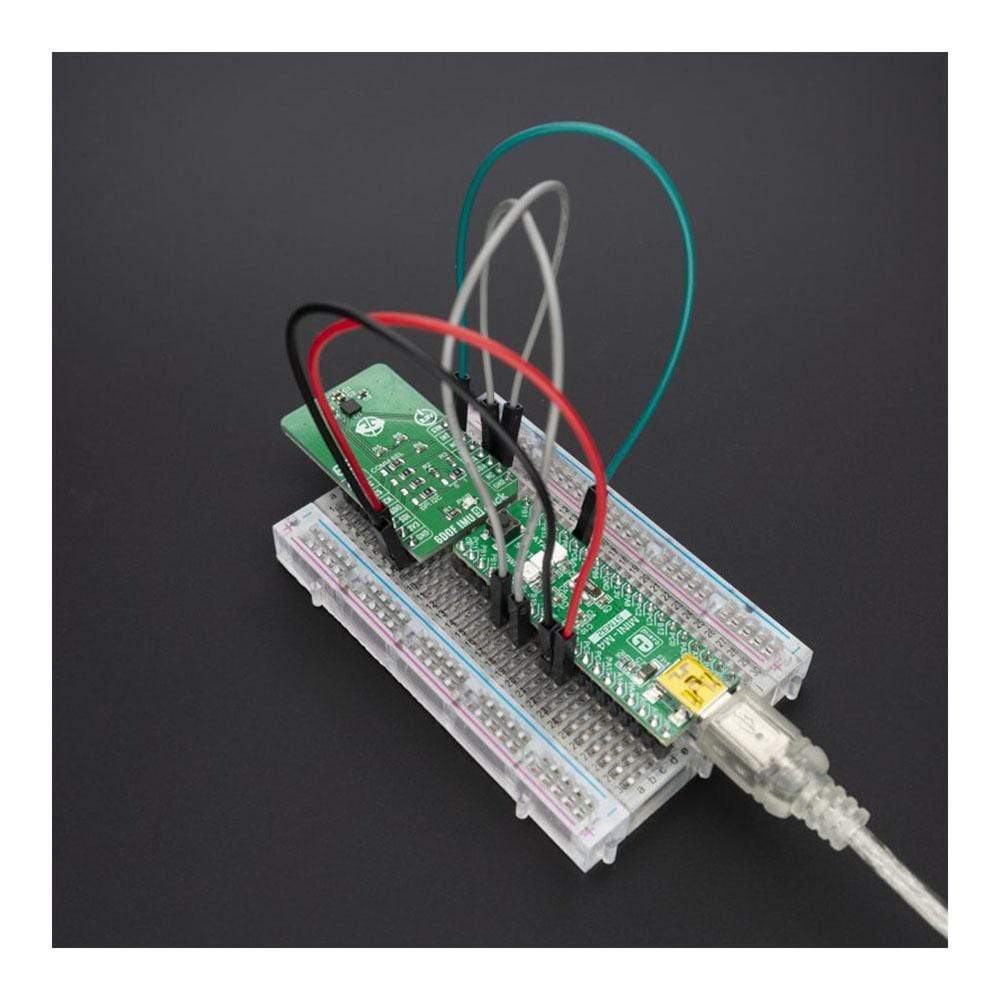
Overview
Das 6DOF IMU 9 Click Board™ verfügt über das IAM-20680, ein 6-Achsen-Bewegungsverfolgungsgerät, das ein 3-Achsen-Gyroskop und einen 3-Achsen-Beschleunigungsmesser von TDK InvenSense kombiniert. Eine Kombination der beiden am häufigsten verwendeten Bewegungssensoren ermöglicht eine vollständige 6D-Erfassung. Maßgeschneidert für Industrie 4.0.
Dieses Click Board™ kann für Automobilanwendungen und Navigationssysteme als Hilfsmittel für Koppelnavigation, Heckklappenbewegungserkennung, genaue Fahrzeug-zu-Fahrzeug- und Infrastrukturortung, 360°-Kamerastabilisierung, Autoalarmanlagen, Telematik und Versicherungsfahrzeugverfolgung verwendet werden.
General Information | |
---|---|
Part Number (SKU) |
MIKROE-3827
|
Manufacturer |
|
Physical and Mechanical | |
Weight |
0.018 kg
|
Other | |
Country of Origin |
|
HS Code Customs Tariff code
|
|
EAN |
8606018719686
|
Warranty |
|
How Does The 6DOF IMU 9 Click Board™ Work?
The 6DOF IMU 9 Click Board™ is based on the IAM-20680 is a 6-axis MotionTracking device for Automotive applications from TDK, that combines a 3-axis gyroscope and a 3-axis accelerometer in a small 3x3x0.75mm (16-pin LGA) package. It also features a 512- byte FIFO that can lower the traffic on the serial bus interface and reduce power consumption by allowing the system processor to burst read sensor data and then go into a low-power mode. IAM-20680, with its 6-axis integration, enables manufacturers to eliminate the costly and complex selection, qualification, and system level integration of discrete devices, guaranteeing optimal motion performance.
The IAM-20680 has many features including the Digital-output X-, Y-, and Z-axis angular rate sensors (gyroscopes) with a user-programmable full-scale range of ±250 dps, ±500 dps, ±1000 dps, and ±2000 dps and integrated 16-bit ADCs, Digital-output X-, Y-, and Z-axis accelerometer with a programmable full scale range of ±2g, ±4g, ±8g, and ±16g and integrated 16-bit ADCs and a User-programmable digital filters for gyroscope, accelerometer, and temperature sensor.
The IAM-20680 includes the following additional features such as minimal cross-axis sensitivity between the accelerometer and gyroscope axes, a 512-byte FIFO buffer enables the applications processor to read the data in bursts, with a digital-output temperature sensor and the MEMS structure hermetically sealed and bonded at wafer level.
The 6DOF IMU 9 communicates to a system processor using either a SPI or an I2C serial interface. The IAM-20680 contains a 512-byte FIFO register that is accessible via the Serial Interface. The FIFO configuration register determines which data are written into the FIFO. Possible choices include gyro data, accelerometer data, temperature readings, and FSYNC input. A FIFO counter keeps track of how many bytes of valid data are contained in the FIFO. The FIFO register supports burst reads. The interrupt function may be used to determine when new data are available. The IAM-20680 allows FIFO read in low-power accelerometer mode.
6DOF IMU 9 Click Board™ supports both SPI and I2C communication interfaces, allowing it to be used with a wide range of different MCUs. The communication interface can be selected by moving SMD jumpers grouped under the COM SEL to an appropriate position (SPI or I2C). The slave I2C address can also be configured by an SMD jumper when the Click Board™ is operated in the I2C mode an SMD jumper labelled as ADD LSB is used to set the least significant bit (LSB) of the I2C address.
Due to the IAM-20680, the 6DOF IMU 9 Click Board™ can be used for automotive applications and navigation systems aids for dead reckoning, lift gate motion detection, accurate location for vehicle to vehicle and infrastructure, 360º view camera stabilization, car alarm, telematics and insurance vehicle tracking.
SPECIFICATIONS
Type | Motion |
Applications | Automotive applications and navigation systems aids for dead reckoning, lift gate motion detection, accurate location for vehicle to vehicle and infrastructure, 360º view camera stabilization, car alarm, telematics and insurance vehicle tracking |
On-board modules | IAM-20680, a 6-axis MotionTracking device that combines a 3-axis gyroscope and a 3-axis accelerometer, from TDK InvenSense |
Key Features | 512-byte FIFO buffer, MEMS structure hermetically sealed and bonded at wafer level, Digital-output temperature sensor |
Interface | I2C,SPI |
Compatibility | mikroBUS |
Click Board™ size | M (42.9 x 25.4 mm) |
Input Voltage | 3.3V |
PINOUT DIAGRAM
This table shows how the pinout on 6DOF IMU 9 Click Board™ corresponds to the pinout on the mikroBUS socket (the latter shown in the two middle columns).
Notes | Pin | ![]() |
Pin | Notes | |||
---|---|---|---|---|---|---|---|
NC | 1 | AN | PWM | 16 | SYN | External sync | |
NC | 2 | RST | INT | 15 | INT | Interrupt | |
SPI Chip Select | CS | 3 | CS | RX | 14 | NC | |
SPI Clock | SCK | 4 | SCK | TX | 13 | NC | |
SPI Data OUT | SDO | 5 | MISO | SCL | 12 | SCL | I2C Clock |
SPI Data IN | SDI | 6 | MOSI | SDA | 11 | SDA | I2C Data |
Power Supply | 3.3V | 7 | 3.3V | 5V | 10 | NC | |
Ground | GND | 8 | GND | GND | 9 | GND | Ground |
ONBOARD SETTINGS AND INDICATORS
Label | Name | Default | Description |
---|---|---|---|
LD1 | PWR | - | Power LED Indicator |
JP1-JP4 | COM SEL | Right | Communication interface selection: left position SPI, right position I2C |
JP5 | ADD LSB | Right | Save I2C address LSB selection: left position 0, right position 1 |
Frequently Asked Questions
Have a Question?
Be the first to ask a question about this.